Choosing the right Print and Apply technology for your business
23rd May, 2016
Choose the right Print and Apply Coding Technology
Download the full visual Secondary Packaging Coding Guide,
Label Print ApplyWith the upswing in demand for dynamic multi-product factory lines and an ever-growing range of print and apply coding technologies, it is now more important than ever to keep your factory equipped with machines capable of staying several steps ahead of the pack.
Fear not! Our in-house team of technology experts have evaluated a handful of popular and emerging methods of application, so you don’t have to!
Pre-printed boxes and inkjet printer
One method of printing onto secondary packaging is to print variable data onto the substrate using an online inkjet printer.
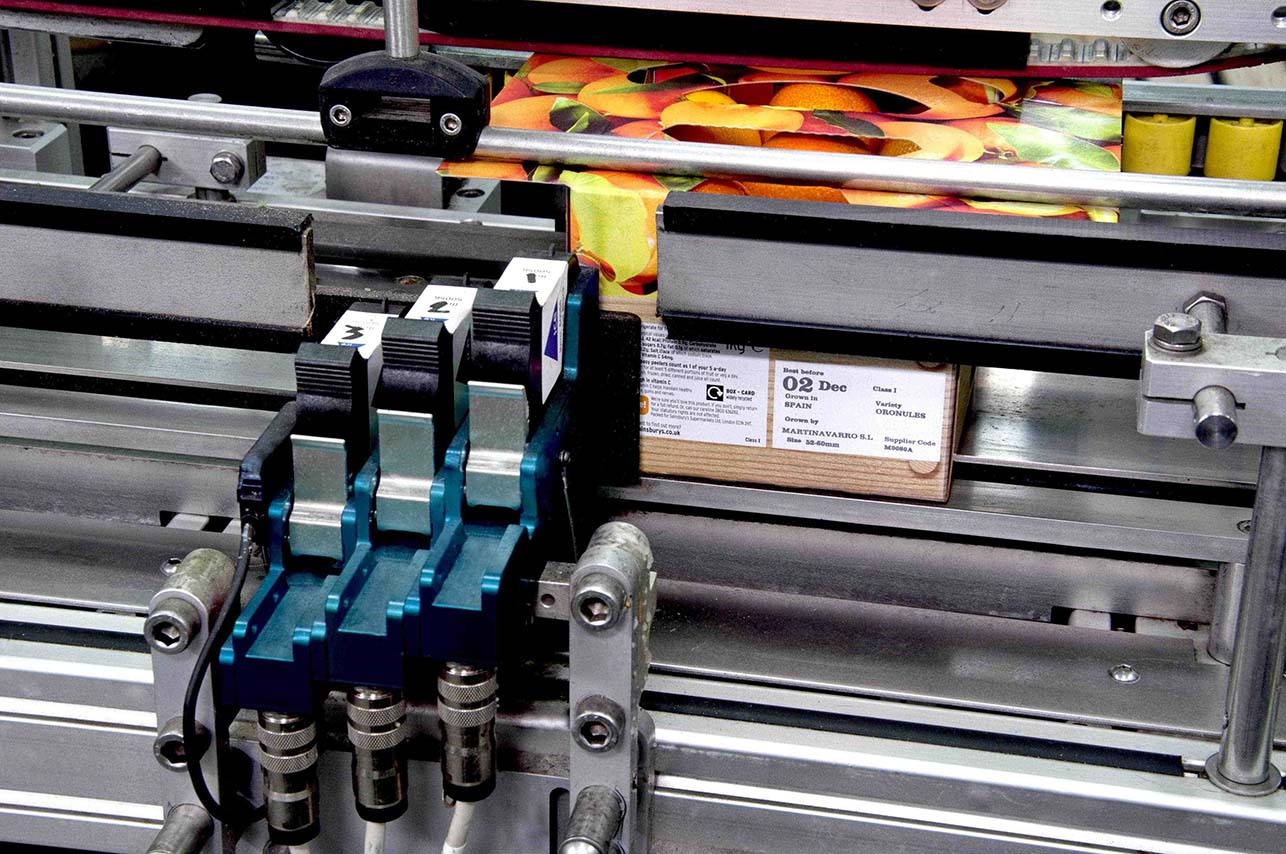
Pros
The online print requirement is relatively low cost and is simple to set up and operate.
Cons
The cost of pre-printing on boxes is relatively high, particularly when there are a large number of product varieties. A variety of pre-printed boxes will also need to be stored on-site and could lead to stock management issues, reducing the flexibility of your production line.
Large character marking (LCM)
Another method would be to print information on a cardboard substrate with a large print area.
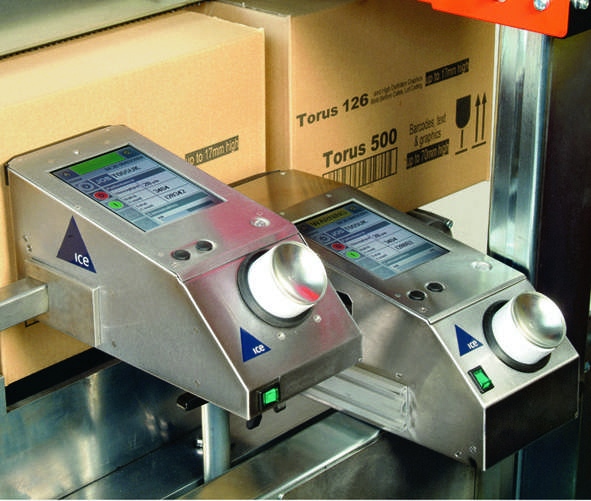
Pros
This option gives you the ability to combine the requirements for variable data and article information all together on one label. An LCM system also eliminates the need to keep an inventory of pre-printed stock, the requirement of a print room and requires a considerably smaller amount of human resource than other methods of printing.
Cons
It is difficult to achieve desired ANSI print quality grades on recycled board. Often ANSI grade C is the highest grade that can be achieved on recycled board.
Print labels off-line and hand-apply
Labels can also be printed off-line in a print room and applied by hand.
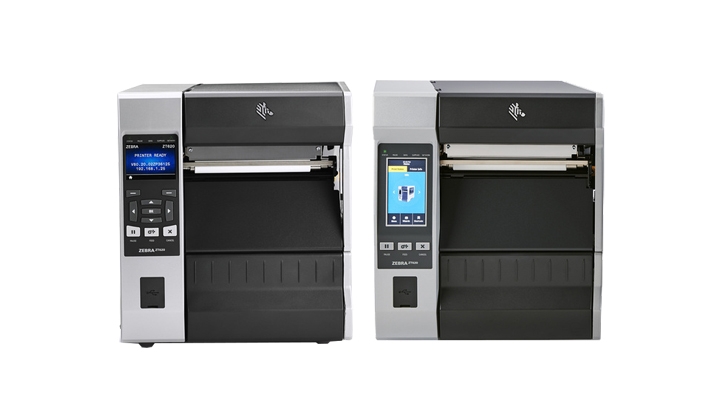
Pros
This method is relatively low cost and labels can easily be applied with a conventional desktop label printer. No on-line equipment means no downtime or on-line issues and fewer issues with maintenance.
Cons
A small workforce is required to hand apply labels and conventional desktop label printers typically print at low speeds. The hand apply method increases the opportunity for human error and waste. An increase in demand could also make the whole process inefficient.
Print labels offline and apply using an applicator
Print labels in a print room off-line and use a label applicator to apply the labels on the packaging line.
Pros
This option is relatively low cost and an automated label applicator reduces the requirement of human resource working in a print room. Similarly to the last method, a cheap conventional desktop label printer can be used, reducing downtime and the requirement of maintenance.
Cons
Labels print at typically low speeds and human resource increases the risk of label wastage. This method also requires two different processes, one on-line and the other in the print room, therefore increasing the overall labour requirement.
Print and Apply label applicator (LPA)
Labels are printed on-line and applied at the time of printing.
Pros
This option gives you the flexibility to produce what you want, when you want, when you need it, with on-line digital capabilities. An LPA system can also combine the requirements for variable data and article information on one label, does not require an inventory of pre-printed boxes to manage, does not require a print room, requires less human resource to manage the process, is able to print at the ANSI A grade to comply with supermarket requirements and can be tracked through unique codes generated by the printer software.
Cons
The cost of labels and ink (ribbon) may be slightly higher than printing directly on to the box.
Related
Clearmark Extends Coding and Labelling Portfolio with Zebra Off-line Printer Range
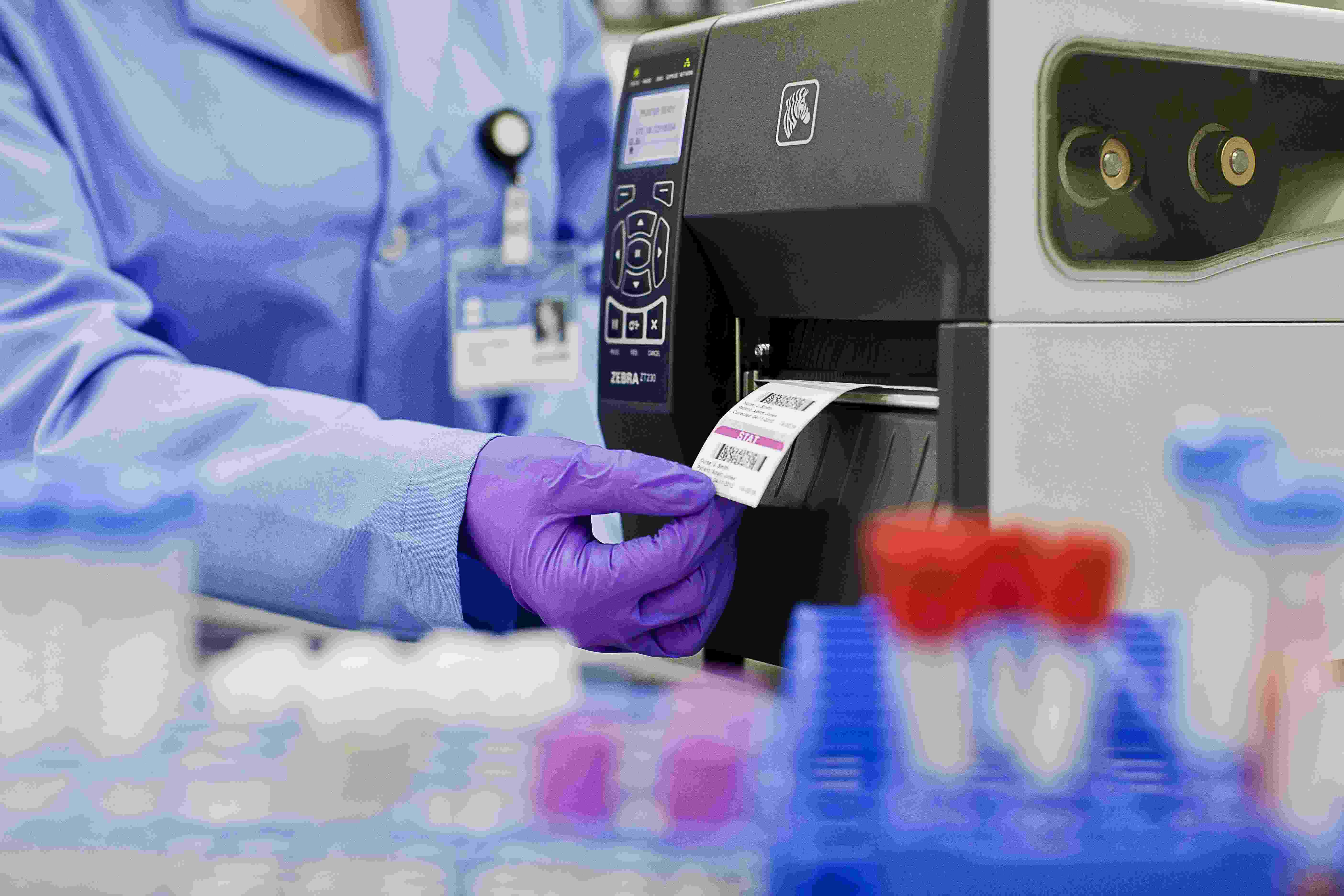