Hot Foil vs Thermal Transfer Printing: Why Switch?
12th April, 2019
Both Thermal Transfer Overprinting (TTO) and Hot Foil Stamp apply a variety of information onto flexible packaging. However, there are significant differences between the two technologies. We take a closer look at both technologies and why making the switch to thermal transfer overprinting can improve your production line and save you money.
How do the two compare?
Hot Foil Stamp
• Works like an analogue printing press, where a manual type is used for printing
• Manual operation required
• Melts ink onto the substrate from a heated type template pressing onto a ribbon
• Can work on continuous and intermittent applications
Thermal Transfer Overprinting
• Thermal transfer printhead makes contact with the flexible substrate
• Miniature printing elements located under a class coating are precisely heated
• Software/centrally controlled to create digital real-time images
• Works on both continuous and intermittent applications
One of the biggest benefits customers see when they switch from hot foil to thermal transfer printing for flexible packaging lines is the reduction in operating costs. Whilst the initial investment for a hot foil stamp printer is generally cheaper than a thermal transfer printer, long term, the thermal transfer overprinter operational costs and consumables are cheaper.
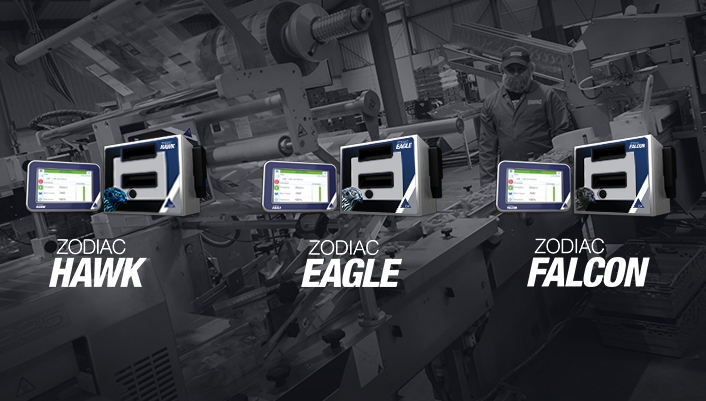
Ribbon Costs and Reducing Ribbon Waste with Thermal Transfer Overprinting
Both technologies require ribbon to operate and can be the major portion of running costs, however, hot foil stamp ribbons are more expensive as hot foil stamp ribbon is thicker than thermal transfer ribbon, as it needs to withstand the high-temperature contact.

Thermal transfer systems also consume less ribbon than hot foil stamp printers as the TTO technology provides much tighter control of the ribbon movement, maximising usage.
Hot foil stamp printers leave larger gaps between print images, which can result in wasting a large portion of the ribbon itself. Not only are TTO ribbons much longer (1.2km vs 300m) TTO technology also allows for a ‘ribbon save’ feature that minimises the gap in prints as much as possible.
Downtime and Physical Part Replacement
Typically, hot foil stamp ribbons are more prone to breakages between 1-3 times per shift, which can cause, on average, 15-20 mins downtime and waste whilst the ribbon is replaced.
Due to the small size of hot foil stamp type, the individual characters can be quite easy to lose, and will need to be replaced periodically. In some instances, a full set of type may need to be replaced, even when only one new character is required.
Due to the advantages of thermal transfer technology, whilst the printheads themselves require replacement, the digital technology negates the need for any type expenses and all changes can be controlled through ICE CLARiSOFT label design software on-screen. In addition to the cost savings overall, thermal transfer overprinting machines are much smaller and can integrate seamlessly with your current production line.
Here at Clearmark, as well as providing the highest quality ICE products, including the range of Zodiac Thermal Transfer Printers, we offer bespoke integration solutions to suit the needs of your factory. Speak to one of our coding and marking experts today on enquiries@uk.interactivecoding.com or 01159 640144.
Related
Printing on Flexible Packaging with Thermal Transfer Printing
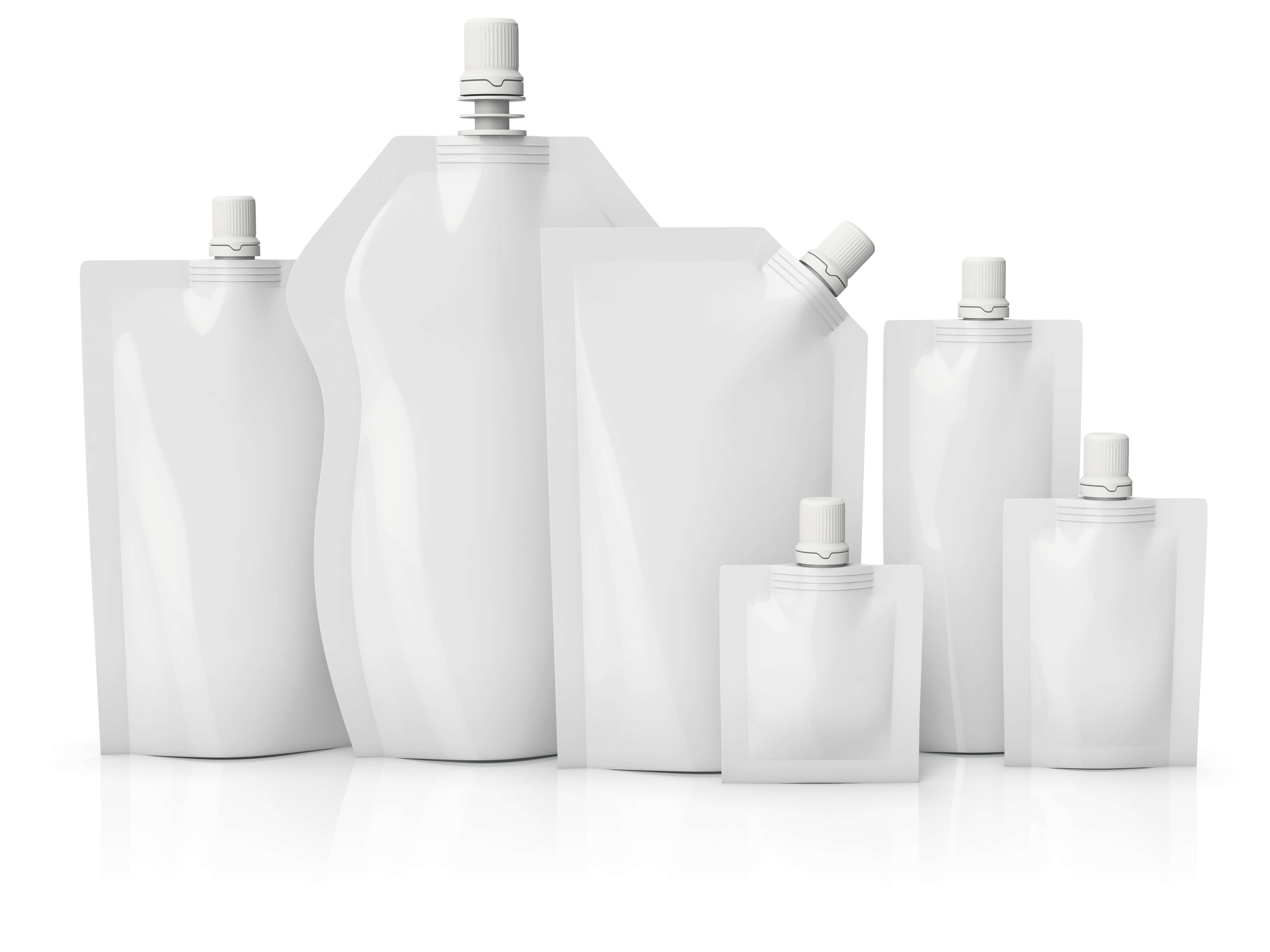