Net Zero: Clever OWL preys on recyclable net and tag coding packaging trends
7th November, 2022
Clearmark has mastered the challenge of efficiently over-printing watchstrap label bands on the uneven surface areas used in net and weave packaging applications, including citrus, fresh produce, seasonal confectionery, shellfish, nuts and firewood bags.
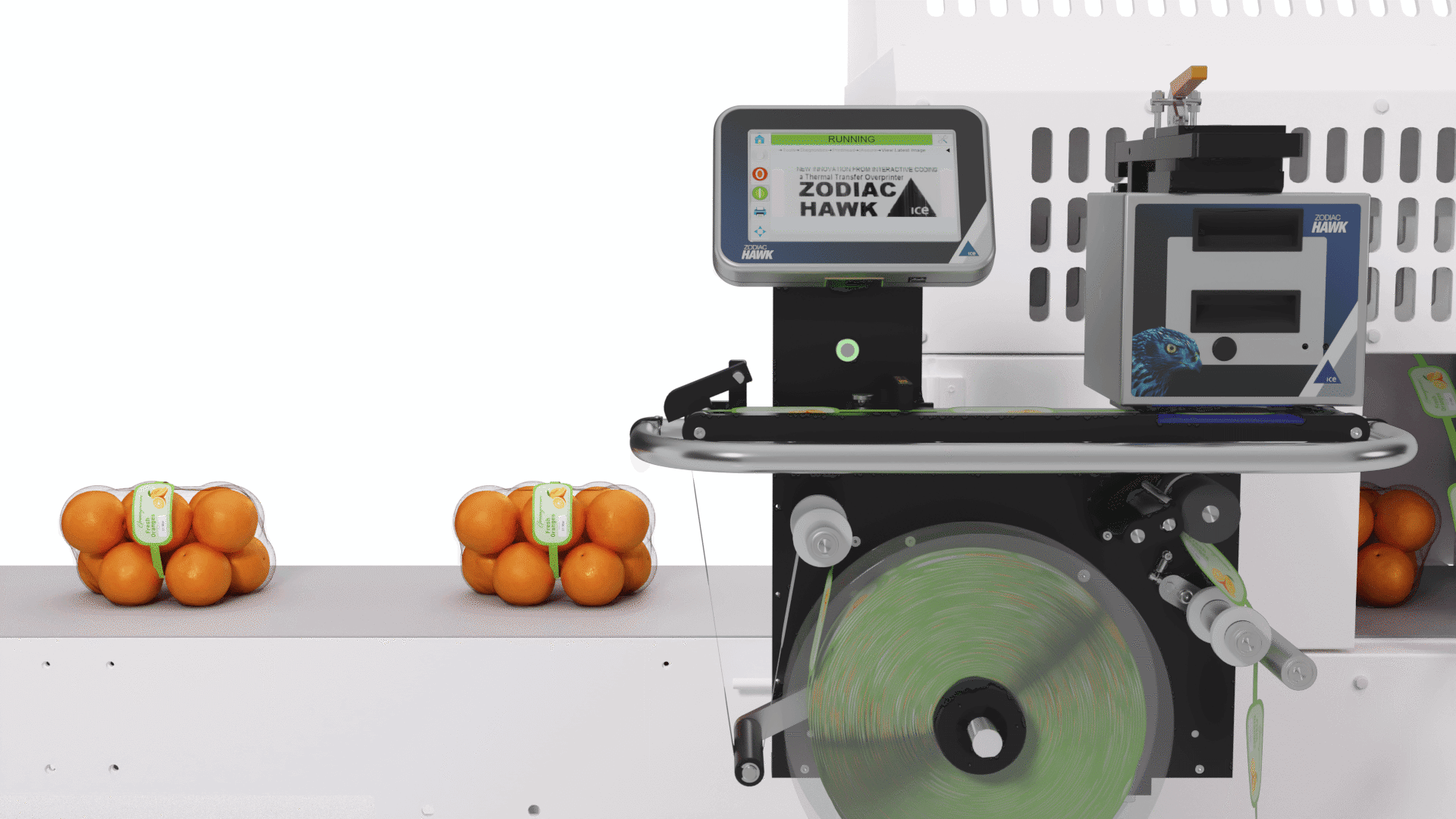
Having observed rising demand for a reliable, fast and accurate net and tag coding system, Clearmark has engineered an innovative new Overprinting Watchstrap Labeller (OWL) system. Designed to address the challenge of tension causing the thin section band of watchstrap labels to snap when stress is applied during the placement on textured surfaces, the compact Zodiac OWL delivers consistent label printing at rates exceeding 60 packs per minute. Simultaneously, the new system optimises quality control by ensuring netted products are coded perfectly to reduce waste and retailer returns.
Built around the ICE Zodiac Hawk thermal transfer printing concept, Clearmark’s introduction of the Zodiac OWL enables netting packaging environments to efficiently harness the same proven reliability, flexibility and accuracy benefits, including the constant monitoring and reporting of print code quality. For increased flexibility, the OWL watchstrap label dispensing system can also be integrated with Clearmark’s ICE Zodiac Falcon and Eagle product ranges.
Motion sensitive
Matching the pace of current net packaging lines, the OWL has been specifically designed to cater to a certain label type. Comprising a narrow and wide section, Chris Simpson, Technical Project Manager. expounds the delicate application process and why it’s so critical not to place too much stress on watchstrap labels. “If too much tension is applied during the label dispensing process, there’s a higher likelihood of the narrow section snapping.”
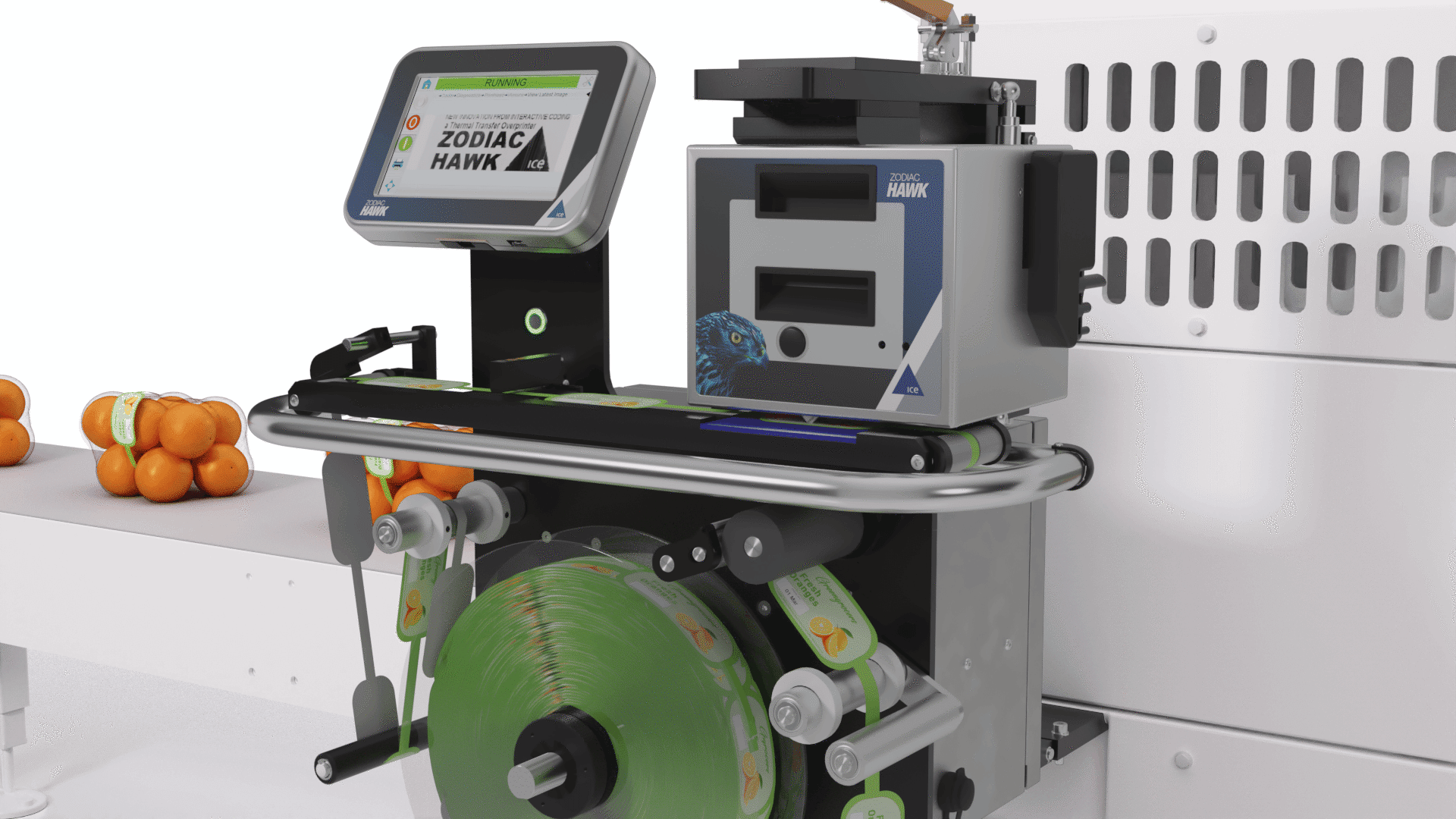
In another clever feat of engineering, Clearmark addressed this issue by integrating the drive system into the printer bracket. The result – labels are dispensed and printed using thermal transfer in one continuous and synchronised motion.
“Because the OWL is electronically integrated with the netting machine, each time a netted bag is made, the OWL feeds another printed label into the loop,” explains Chris.
Should the netting machine demand more labels than have been supplied into the loop, the OWL’s lifting arm will instantly detect the slightest tension. This motion sensitive feature prompts the in-feed netting machine to pause to prevent the narrow web from snapping.
Intelligent intervention
Rather than investing in additional expensive vision systems to monitor the quality of labels, the OWL system also features iAssure. This internal print checking system assesses in real-time the spent ribbon after each code has been produced to determine whether the print quality meets the set standards. If the code is deemed to be unacceptable, a signal is instantly dispatched to reject the netted pack. Should the print quality fault persist, the system will flag this trend and halt the line entirely until the issue is resolved.
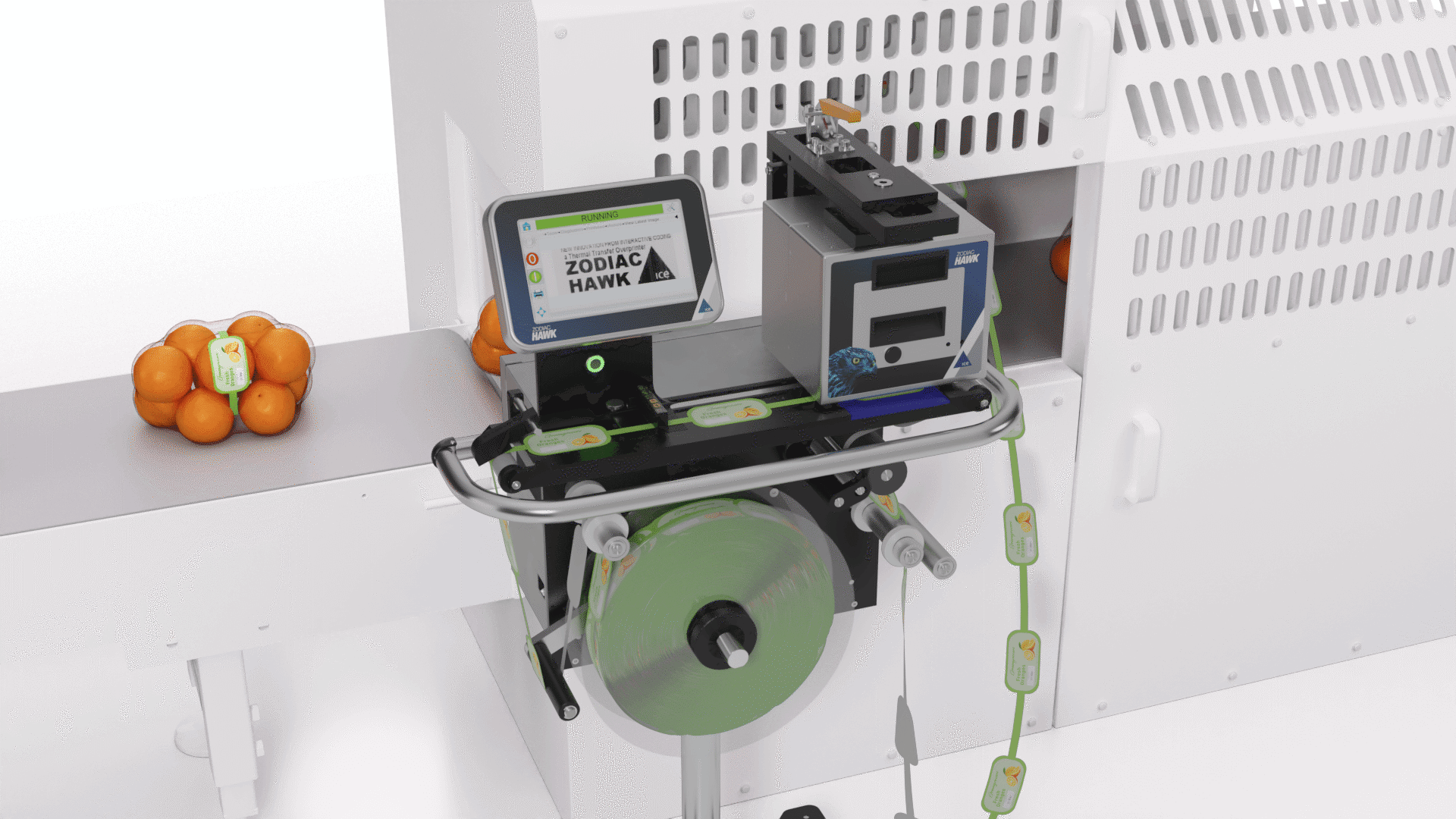
“By providing early intervention, production disruption and downtime can be minimised. This also reduces the likelihood of a product recall and a heavy retailer fine,” notes Chris. Operators can easily measure production quality via the CLARiTY touchscreen and can view label information in real-time to assess print quality and drive further efficiency improvements.
An illuminated feed button also provides operatives with visual cues alerting them when a specific action or human intervention is required. For example, prompting operatives to manually feed a label into the loop or highlighting that the 1200 metre-long thermal transfer ribbon needs changing. Once resolved, operatives simply press the reset button and the net packing line restarts again.
Supporting efficient product changeovers is the CLARiSUITE operating system. Making it straightforward for users to create and switch label design templates.
Conserving productivity
Measuring just 1280mm high, 680wide and 420mm deep the compact OWL system can be easily integrated into existing packaging set ups, either as a freestanding solution or within the netting machine itself. Running at 60 packs per minute, the system effortlessly keeps pace with today’s netting systems reports Chris. However, the OWL also has the in-built capacity to match future netting line speeds.
Summarising the trends in netted products and how these are aligned to eco-packaging developments, Chris adds: “Mesh and net produce bags are increasingly being made using natural and compostable materials rather than plastic netting, which is increasingly their popularity further. In fresh produce especially, the mesh design promotes air flow. Which reduces the risk of spoilage due to condensation and consequently reducing food waste. Furthermore, most UK supermarkets now accept empty net bags at their packaging collection points.”
Those that aren’t returned to retailers are often upcycled by savvy householders and lifestyle influencers, with empty netted produce bags being turned into everything from dish scrubbies to winter bird feeders.
View the machine in action here.