ICE Vulcan Labeller finds its Vocation in craft beer market
9th September, 2021
Clearmark Solutions has partnered with the enterprising Vocation Brewery to install its first ICE Vulcan print and apply labelling system at the Halifax factory, guaranteeing to meet GS1 criteria, saving on cost, waste and increasing turnover through quicker print runs to label boxes of beer for shipment to the top five UK multiples.
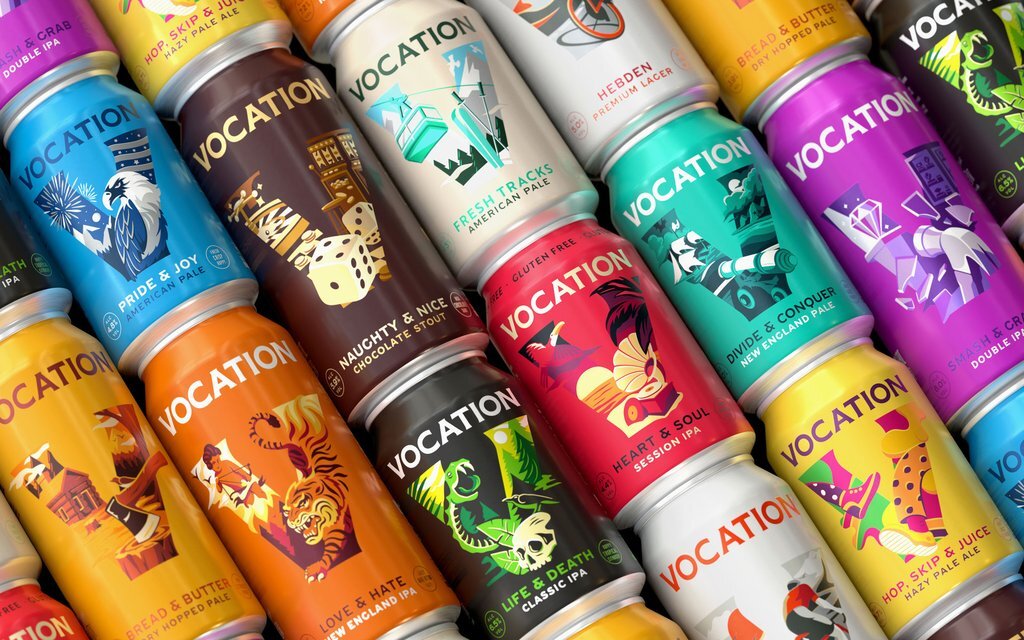
Last year, with sales of craft beers soaring due to lockdown restrictions when the nation’s drinking habits became home-based1, Vocation Brewery had to look at new, faster ways of applying labels to their boxes whilst being compliant with GS1 regulations. Previously, labels were printed using a desktop printer and applied by hand, meaning the process was slow and the labels were not always clearly printed or positioned in a neat, uniform way. Now with the investment in the ICE Vulcan print and apply labeller, the cost to label each box of craft beer has dropped by an incredible 90%, costing the brewery just half a penny per label. Print speeds can reach over 120ppm with a label capacity of 17,000 labels, more than twice the capacity of other labelling systems.
Since John Hickling established Vocation Brewery in a rebuilt chicken shed in 2015, it has gone from strength to strength, successfully employing 60 staff, selling up to 14 million cans per year. Vocation Brewery won its first listing in Tesco stores in 2016 and now supplies standard and bespoke product lines to multiple retailers including Asda, Sainsbury’s, Waitrose, Booths and Marks & Spencer.
The ICE Vulcan print and apply labelling system has a non-pneumatic ‘air-less’ design using a unique direct apply method which allows for extremely accurate label placement without the need for an applicator. The system boasts Intelligent Motion™ technology which enables precise automatic control of components and an 80% reduction of wear parts that traditionally caused unexpected downtime and cost.
Dan Sutcliffe-Tasker, Head of Packaging, Vocation Brewery, said: “Growth in supermarket chains and orders for seasonal and one-off product lines has seen production increase to 60,000 hectolitres this year, up from 10,000 when we first started, that’s approximately 12-14million cans this year.”
“Everything sent to the retailer has to be boxed and labelled. We produce about 30 pallets a day, with 100 or 200 cases on each pallet. Anything other than our core brand has to have a custom label on it. Since automating our labelling process we’ve had zero defects - the ICE Vulcan print and apply system is 100% fool-proof and in hindsight we should have automated sooner.”
With Vocation launching pale ale specials such as Tr-hop-ical in a short time frame, Vulcan’s quick changeover, flexibility and print and placement accuracy came into its own. Vocation had to accurately label generic boxes which met GS1 specifications for warehouse use and transit. Prior to installing the ICE Vulcan, Vocation used a desktop thermal printer and then hand applied the labels, which was a laborious job. With the release of 51 new products last year, Vocation had to up their ante and find a more accurate and efficient labelling method.
In the early days Vocation had 26 pallets returned as a result of incorrect barcodes and human error, causing the brewer to re-call and re-label the goods, which was both time consuming and costly. With the ICE Vulcan system, using CLARiSOFT™ label design software, labels are designed and programmed for the operator to select using the CLARiTY operator touchscreen. CLARiTY allows operators to select the job from a list or pre-programmed jobs, eliminating operator intervention and human error.
The ICE Vulcan has in built tutorials to help operators perform functions such as changing the print head, thermal transfer ribbon and label reel with built in print save options which means no ribbon is wasted in between prints.
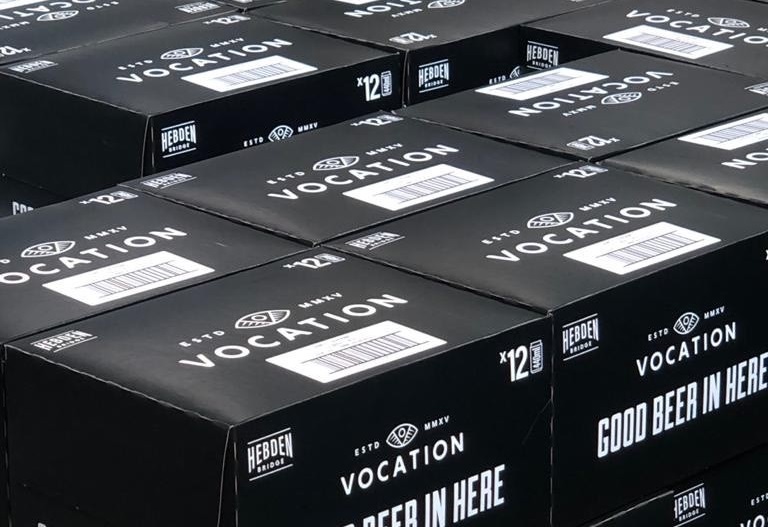
Vocation compared systems but were most impressed with Clearmark’s unique direct apply application rather than a blown on label which can create creased labels . Thanks to a height adjustable stand, the system can accommodate changes to box size in just a few seconds.
“The main concern for us was individual placement of the label. There is no way a human operator can stand there on an eight-hour shifts and hit the same mark every time, especially when things were operating so quickly. We needed stability and guaranteed repeatability that automation is known for,” added Dan.
“Since the ICE Vulcan was installed in March, accuracy has improved dramatically with no issues. The print quality is also of a higher standard as the desktop printer ink sometimes faded due to condensation on the craft board from the temperature, turning the black print grey. But we have had no issues like that with the ICE Vulcan”.
The project took just 10 weeks to complete from initiation to installation. Thanks to surveys and CAD drawings, the small footprint ICE Vulcan slotted into the existing factory layout with little disruption to production. The ICE Vulcan has allowed them to meet the demands posed by the increase of orders both online and via supermarket distribution.
Dan concludes: “The feedback from clients both externally and internally in the shop and warehouse, is that the products are much easier to identify now everything has a uniform label on it. We had to pass a Marks and Spencer transit trial to scan the barcodes individually before we sent the boxes and we passed it with flying colours. Everything meets GS1 global standards for barcodes, which has encoded information such as product numbers, serial numbers and batch codes as well as product descriptions”.
It is not the first time Clearmark has supplied its ICE Vulcan print and apply labelling solution to a craft beer brewery and since this latest installation it has received a number of calls from other breweries expressing interest in the Vulcan print and apply system.
1 https://www.theguardian.com/business/2020/jul/21/uk-grocery-sales-covid-19-outbreak-local-shops