Choosing the right coding and labelling technology
Introduction
The manufacturing industry is facing many modern challenges. Constant changes in legislation, the uncertainty of Brexit, technology advancements and automation in the factory are all factors which need to be considered when kitting out your production line.
Ongoing changes make it absolutely crucial to know all of the available options before choosing the right coding and marking technology. Initial analysis, demonstrations and expert advice can be the difference which ensures your factory runs more efficiently at the right cost, ensure you have both happy customers and stakeholders.
What factors do I need to consider?
What you're coding on to
The most important factor; materials and substrates. Not all coding and marking technologies are suitable for all substrates. It’s important to get this right from the start.
Speed of your production line
Some solutions move faster than others, offering more packs per minute where required, however this can be a detriment to the print quality on some technology solutions. Identify which is more of a priority for your application – speed or quality.
Print quality and readability
Labelling legislation and distributor requirements may determine this for you, it’s important to think about the customer and the product, For example, in the food industry, products with a short shelf life may require more data on a barcode or legally require a permanent use by date to be printed directly on to the packaging.
Coder features
Variable data, embedded data, QR codes or graphics will all determine the size, type, speed and style of coding and marking technology required.
What is Thermal Transfer Overprinting (TTO)?
How it works
Thermal Transfer Overprinting (TTO) uses a fixed width thermal printhead to apply ink on to a flexible packaging. This is achieved by contact between the printhead and a platen or roller. Sandwiched between the printhead and the label is a very thin thermal transfer ribbon made of polyester film which is coated on the label side with a wax, wax-resin or pure resin ink.
Typical application
Thermal Transfer Overprinting is the established technology of choice for a wide range of primary packaging coding applications such as vertical and horizontal form fill and seal machines, thermoform and tray sealing machines and a variety of flexible packaging applications. Compared to traditional contact coders such as hot-stamp or roller coders, thermal transfer overprinting traditionally offers superior print quality and lower costs.
Considerations
- The speed and precision of TTO means it is an ideal solution for printing data embedded barcodes or QR codes, which require more detail than some generic barcodes.
- The process allows for printing directly onto packaging media, and is therefore efficient in terms of process and material costs. Print resolution is typically 300 dpi.
- TTO is widely favoured but its application reach does have limitations. Due to the contact print nature of the technology, it is only suitable for flexible packaging and linear print speeds are typically restricted to about 800mm\s if printing barcodes.
How it looks
For further information, see our range of Thermal Transfer Overprinters (TTO), or read our guide on TTO printers here.
What is Thermal Inkjet Printing (TIJ)?
How it works
TIJ is a non-contact process in which liquid ink is “fired” onto the packaging using thermal expansion. The majority of inks are water based and use vaporisation of the water to create the thermal expansion process. These inks must be applied to porous media to give reasonable drying times. Other ink types are available which allow printing onto non-porous media, but these often have longer drying times and may also contain MEK type chemicals.
Typical Application
Thermal Inkjet technology is suitable for both primary and secondary packaging on both porous and non-porous materials.
Considerations
- Thermal Inkjet (TIJ) is a relatively high speed process which provides good resolution and due to its non-contact nature, is suitable for printing onto rigid media.
- Cost per print is comparable to TTO, and due to much of the print technology being contained within the disposable print cartridge, reliability levels are extremely high.
- TIJ is generally limited to use on primary packaging, or small scale secondary packages.
How it looks
For further information, see our range of Thermal Inkjet Printers (TIJ).
What is Print and Apply Labelling (LPA)?
How it works
Print and apply labelling lets users create and apply labels directly onto a product and its packaging. These labels can carry data such as alphanumeric text, barcodes, serialisation, 2D codes, QR codes, addressing, personalisation, graphics and more in an accurate and cost-effective way.
Typical Application
Print and apply labelling is typically used on secondary packaging such as boxes and shrink wrap, labelling products for shipping and storage. Some applications offer direct apply onto both front of pack and corner wrap applications, helping to automate the production line and eliminate human error.
Considerations
- Print and apply labelling can deal with most secondary pack types (e.g. shrink wrapped cases, cardboard cases etc.) with high resolution and print quality, typically 300 dpi using thermal transfer technology.
- The technology is very clean and systems are available which can apply labels to most pack types, on almost all faces of a package.
How it looks
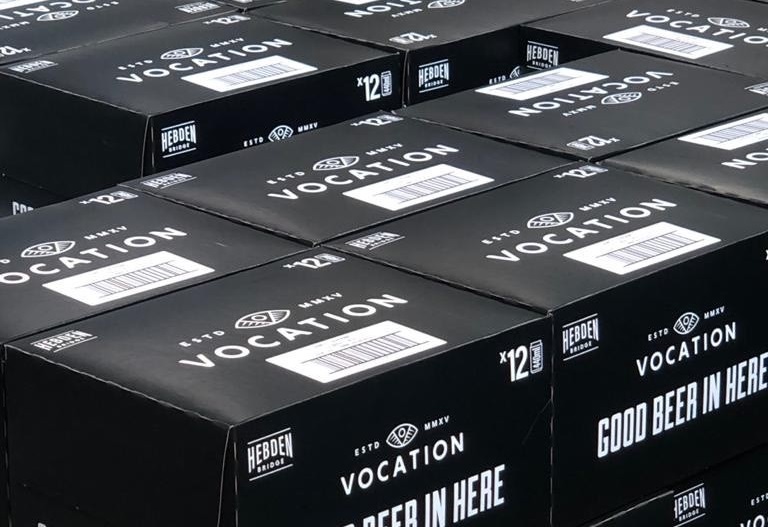
For further information, see our range of Print and Apply Labellers (LPA).
What is Case Coding (LCM)?
How it works
Large Character Markers (LCM) or case coders print variable information, including codes and graphics, directly onto secondary packaging such as cardboard boxes, using inkjet array printing, where a vertical array of addressable jets is used to form an image on a package as it passes.
Typical application
A case coder is an appropriate solution if the substrate you wish to print on is porous, the substrate is white or if the barcode required is an ITF-14.
Considerations
- The technology allows for non-contact printing directly onto porous packaging. It's efficient and has good cost per print figures.
- Print area is typically up to 70mm high with good resolution. Multiple heads may be used to increase print areas, and allow application of information to different sides of a package.
- Since corrugated cases are usually brown, this limits the contrast which can be achieved; meaning the quality of barcodes is not as high as when using a paper label.
How it looks
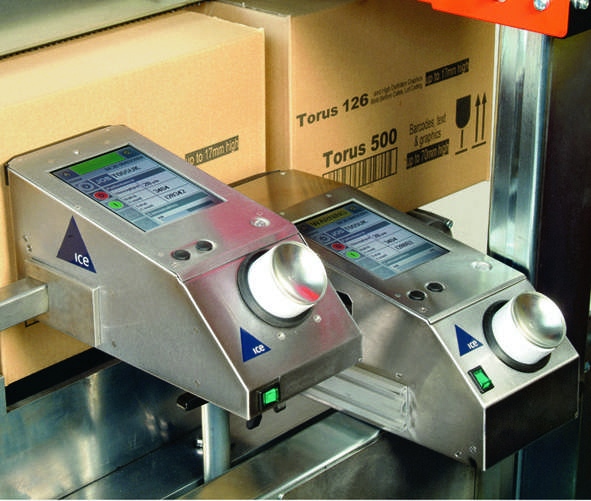
For further information, see our ICE Torus Case Coder.
What is Continuous Inkjet Printing?
How it works
CIJ is another non-contact inkjet process. It uses a stream of charged droplets, which are “steered” to create the printed image.
Typical application
Ideal for marking on flat or curved surfaces, CIJ printing is a non-contact printing method that can utilise a range of CIJ inks to print on almost any substrate whilst it moves along the production line.
Considerations
- It is able to print onto a wide variety of substrates and with a choice of different coloured inks, at very high speeds.
- The resolution of CIJ is not as high as other technologies, In addition, the ink contains a solvent which evaporates after contact with the media to provide fast drying, but this increases the cost of the process, and also the system’s complexity.
- The print area is limited by the print height which can be achieved, and whilst the technology provides very high printing speeds, these will reduce as the number of lines of print increases.
How it looks
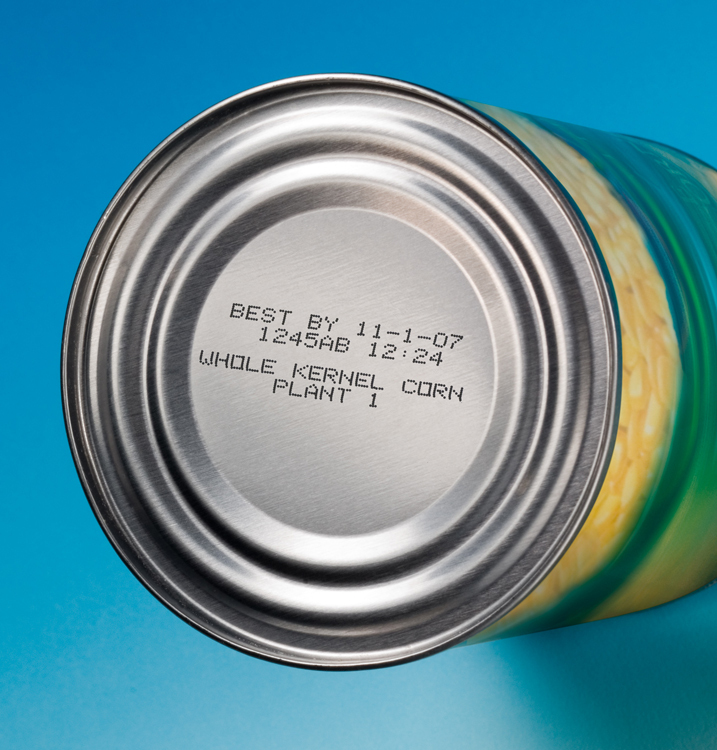
Laser Coding
How it works
The technology uses light at a frequency which will create heat at the point where printing is required. This process is called ablation in which the heat causes removal of a layer of material. This often requires modification to the design and manufacture of the packaging material, and the by-products of the ablation process must be removed, which usually involves fume extraction.
Typical Application
Laser coding and marking machines are ideal for high print volumes which require permanent traceability.
Considerations
- Laser is traditionally more expensive than other coding methods but is able to deliver a permanent code at high speeds, whilst no consumables means lower running costs.
- Laser is cost-effective on high-speed high-utilisation lines, and is a non-contact process and therefore suitable for most packaging types.
- It is possible to apply light-responsive fluids to the packaging media as part of the manufacturing and printing process. This reduces the amount of energy required to print, but it does however add to the cost per print.
- The energy produced by the laser may be harmful to humans and relevant safety systems and guarding will be required. There is also a risk with very light films that the ablation process may penetrate the material.
How it looks
Related Articles
What is a Thermal Transfer Overprinter (TTO)?
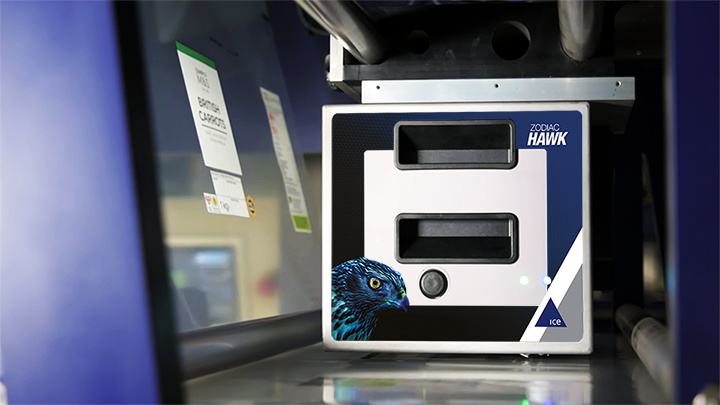
Get in touch
For further advice on all coding and labelling technologies, please get in touch and one of our experts will be happy to help.