Product labelling for the dairy sector
Introduction
To deal with the high demands of dairy production, it is important that manufacturers take time and sound advice on suitable methods to keep production speeds and throughput high, and downtime at a minimum.
Dairy products are required to have variable data labelled onto the secondary packaging before being shipped out from the factory. To keep up with this fast paced and high-demand sector within the food and drink industry, automated labelling technology should be a consideration for manufacturers to support with production. We look at the challenges that dairy manufacturers face and the labelling technology that they can use as part of their production process to overcome those challenges.
The coded data and the placement required
For all dairy products, variable data is required to be coded, marked and or labelled onto its packaging. For example, ‘best-before’ and ‘use-by’ dates are crucial for retailers and consumers to ensure that each product is safe to sell, safe to be consumed, and is of the expected quality.
Dairy manufacturers need to strongly consider where this information is printed onto a pack. For the ‘best-before’ date, it is common to see this information printed on to a seal or lid of a pack. However, these components of the packaging can be discarded by the consumer before they have read this information. As a result, manufacturers have started to add this type of information onto the main body of the pack, where other information is either pre-printed or printed on during production. Similar information must also be added to secondary and tertiary packaging, as well as logistics and traceability information.
Focussing on automated labelling requirements, the equipment needs to have flexible application capabilities to ensure a quality print is applied to the pack, overcoming challenges from small spacing, the packaging material and wet and humid factory conditions.
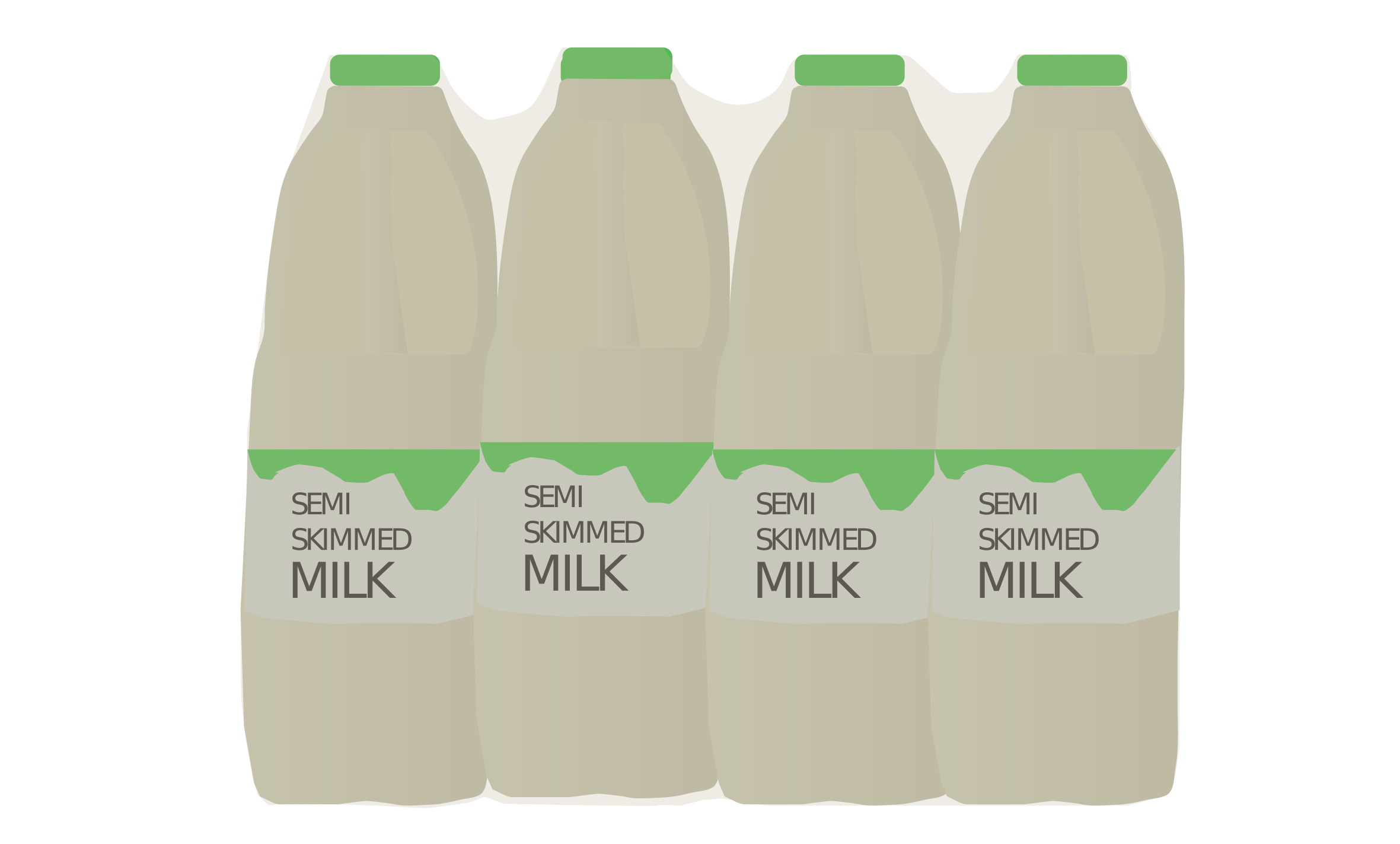
A time-critical production
Shelf life for dairy products vary. Typically, yoghurts will have a shelf life of 1-2 weeks for example, but pasteurised whole milk can be 12 – 14 days if kept below 4°C. Because of the short shelf life of most dairy products, production is time-critical for manufacturers. To add to the complexity of dairy manufacturing; product types, packaging designs and an increasing variety of flavours mean additional measures for changeovers are needed to meet a manufacturer’s requirements.
As a result, maintaining production uptime is a key player for the success of dairy manufacturing, and to maintain a short time to market. To keep up with these requirements, it’s crucial for manufacturers to use labelling equipment that can match fast production speeds, accomplish a high throughput of products, and be versatile enough for product changeovers.
Print and apply labelling (LPA)
Print and apply labelling allows manufacturers to create and apply labels directly onto a product and its packaging. These labels can carry data such as alphanumeric text, barcodes, serialisation, graphics and more in an accurate and cost-effective way. Print and apply labelling is typically used on secondary packaging such as boxes of cheese or a pack of shrink-wrapped milk bottles, labelling products for shipping and storage. It can also be for tertiary pallet labelling, which is the automated application of the logistics labels at the end of the production process, allowing the pallet or logistics unit to be identified and tracked through the entire supply chain.
To meet the demands needed from a dairy productions line, automated labelling suppliers can provide manufacturers with a ‘Zero Downtime (ZDT)’ system in which two labellers are networked together on one line. When the primary labeller runs out of labels, the secondary labeller automatically takes over, meaning operators can replenish the label supply of the primary labeller as production continues even at high speeds.
Having an automated labelling process in general removes the need for manual application by operators. The benefits of using an automated application process over a manual one is that the operators who are working on the lines are able to focus more time on more important tasks during operating hours, such as Total Productive Maintenance (TPM) and quality checks. It’s a more streamlined process that will increase throughput and will apply labels consistently and accurately.
Print and apply labelling has multiple forms of applications to suit the flexibility needed for a dairy manufacturer. Depending on the requirements of the production line, labels can be applied on the sides, top, bottom and front of packs. Please note, it’s important to talk to an automated labelling technology expert before finding a suitable solution for your packaging line as different product types and productions lines will need a specific integration to optimise production.
Can Clearmark help?
Clearmark Solutions has its own secondary labeller, the ICE Vulcan and tertiary labeller, the ICE Vector. We have worked with multiple customers within the dairy industry and have helped them set up an automatic labelling process for their operations with innovative systems that suits their specific requirements. If you have a project that you would like to discuss with us, please contact Clearmark by calling us on 01159 640144 or by emailing us at enquiries@uk.interactivecoding.com.
Related Articles
SSCC for pallet labelling
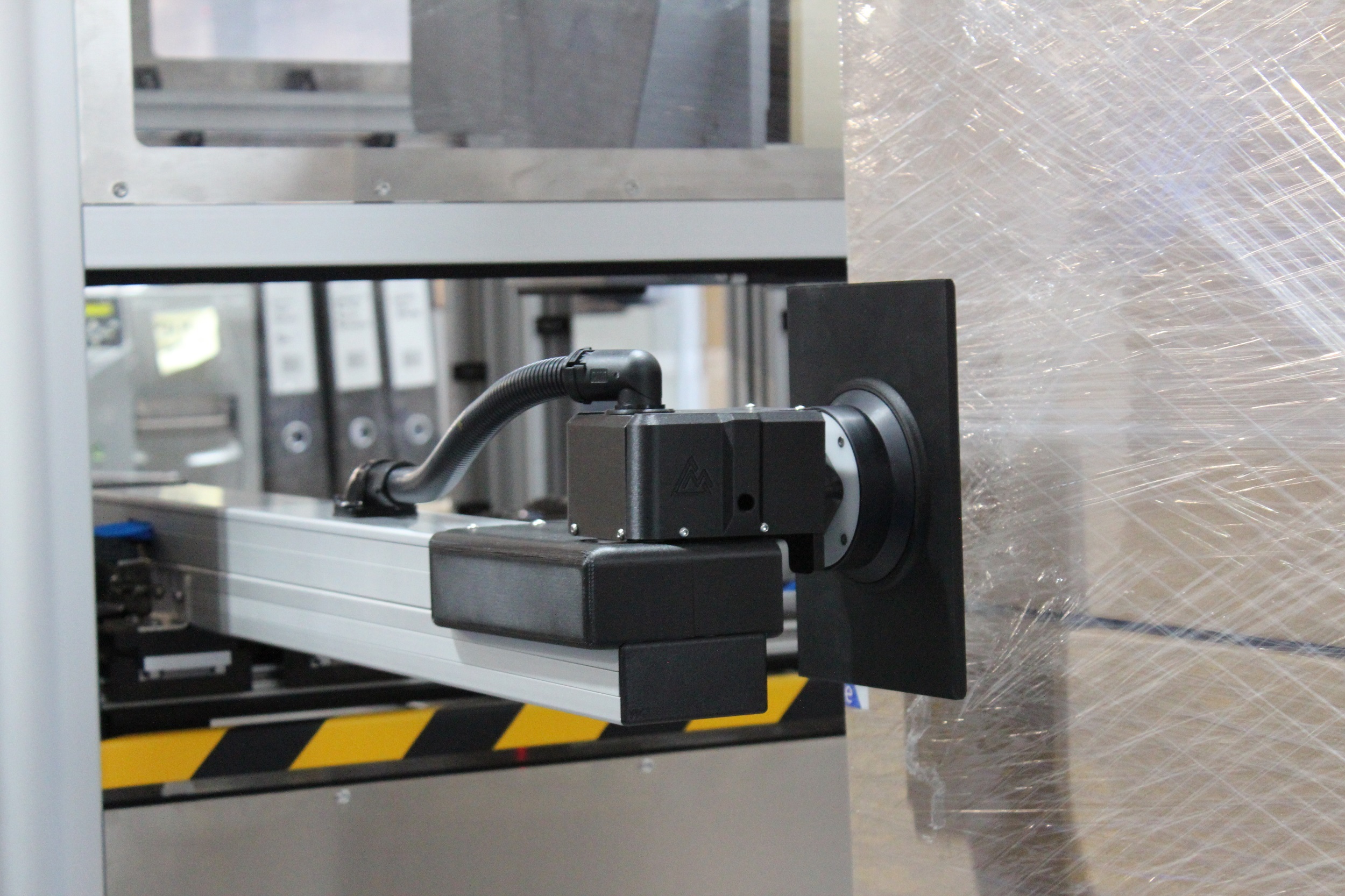
What is automated pallet labelling?
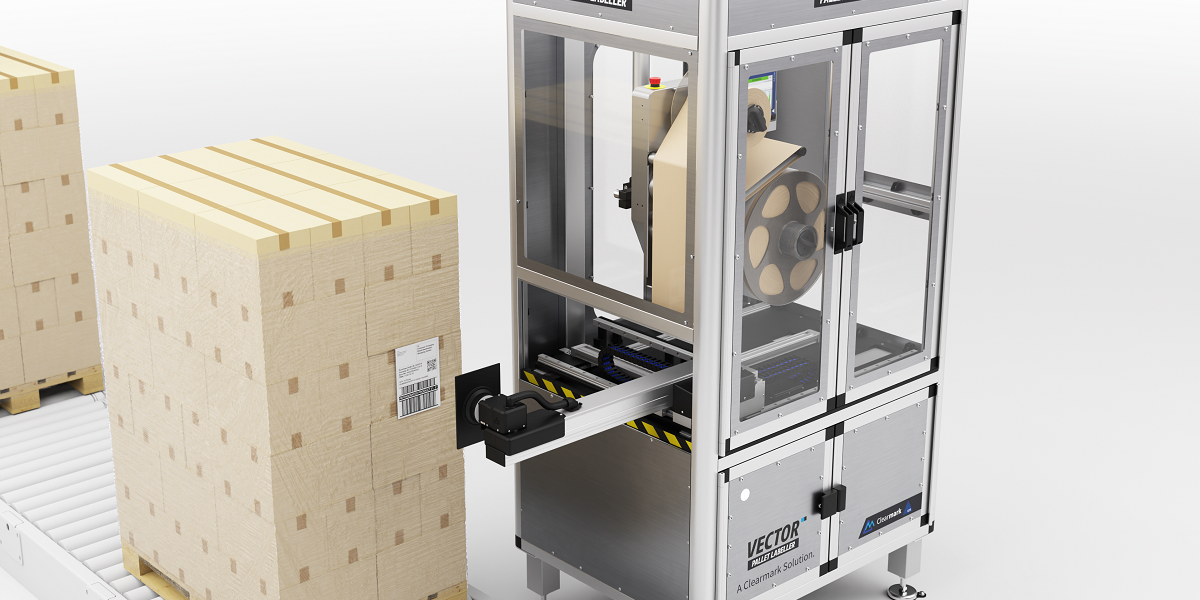
Book a labelling demonstration for your site
If you are interested in a site survey, fill in your details and one of our coding experts will be in touch to talk you through our automated labelling solutions.