What is Industry 4.0?
Introduction
Industry 4.0 is the current trend of automation and data exchange in manufacturing technologies, also referred to as ‘smart factories’ or ‘the industrial internet of things’ (IIoT). Industry 4.0 is the notion that every machine, process and system throughout a factory or business will be integrated and connected to the internet for maximum efficiency within the factory.
Revolution or evolution?
For some, Industry 4.0 is more of an evolution of automation than a full industrial revolution like those of the past. The key technologies for Industry 4.0 are automated robots, system integration, and simulation. These will be supported by technology such as cloud computing, the Internet of Things (IoT), augmented reality, big data and most importantly –developments in cyber security.
What will change?
Most manufacturing environments have a complex Cyber-Physical Production System (CPPS), the integration of other technologies such as monitoring equipment means that all factory equipment will know details such as maintenance plans, configurations and setups, history etc.. Thanks to industry 4.0, the previously internally managed processes can now be accessed around the world.
How does it all work together?
Big data
A fully connected factory will inevitably produce a lot of data, this is known as ‘big data’. In the future, all this information will be sent back to the cloud so it can be analysed by helpdesks and engineers, ultimately allowing developers and engineers to identify any common issues that may be affecting the performance of the overall factory production.
Cloud computing
At every level of production, all data from the factory floor is imported into the ‘cloud’ which can then be stored and accessed from any location. This then allows applications, maintenance and processes to be managed remotely.
Universal standards
An essential component of Industry 4.0 is universal communication standard protocols. Having the communication standards will help connect all parts of the factory together, including devices, production lines as well as the crucial connecting of coders and printers to larger industrial Original Equipment Manufacturer (OEM) machines.
Industrial Internet of Things (IIoT)
Stemming from the term “The Internet of Things (IoT)", where devices are connected over the internet, talking to the user, applications and other devices. Think of items such as an activity tracker worn on the wrist.
The software monitors a users’ activity and then communicates this to the corresponding app on a smart phone or other device. Essentially IIoT is an amplified version of IoT, connecting more networks, larger applications and enabling factories to operate and optimise effectively. Every level of enterprise is now connected.
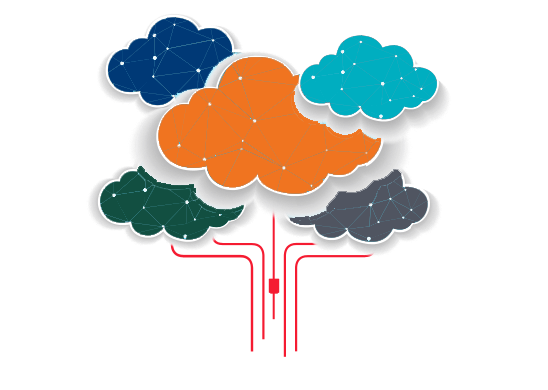
What are the benefits of Industry 4.0?
Efficiency and agility are huge benefits of industry 4.0. When products know their own specifications and can communicate across the entire factory, this will help accelerate processes throughout the production line. Automated factories are already benefitting from improved quality, and with fewer people and room for human error, decisions can be made more quickly, reducing downtime and improving OEE.
What could Industry 4.0 mean for factories?
Fast adaptors to the Industry 4.0 way of thinking will also see the ROI benefits of a fully networked operation. Whilst an initial capital outlay is essential to prepare your factory, the lower operating costs plus less waste and more efficient analysis will improve ROI going forward.
These benefits will naturally be passed onto customers, improving customer satisfaction. A fully networked operation will not only satisfy the needs of customers who require in depth or real time analysis of the production line, but will also allow for any arising issues to be tackled effectively and resolved quickly, ensuring customer trust.
How can coding equipment help?
Using software such as CLARiNET with coding and marking equipment across the factory floor enables printed data to be centralised, providing a single data source for all coding machines in a factory. The fully networked solution not only helps improve Overall Equipment Effectiveness (OEE) but can save time for engineers and production line employees.
“Being able to check a job file from the office and on the coder touchscreen also provides added peace of mind.” – John Tate, Asset Operations Manager at Whitby Seafoods.
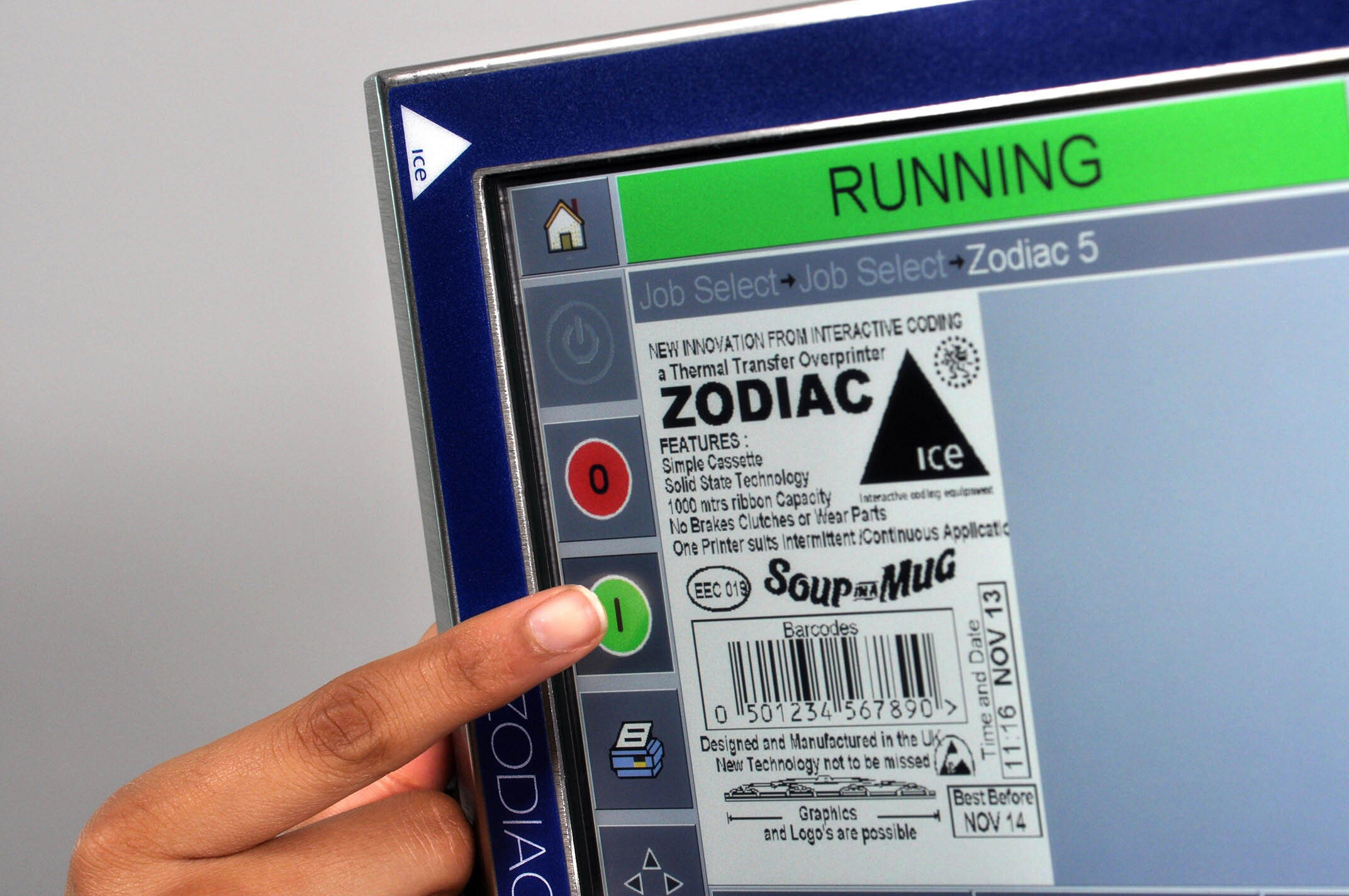
Related Articles
Get in touch
Looking to automate your coding and labelling as part of your smart factory? Contact one of our experts today to help find the ideal solution for your operation.