What is Total Productive Maintenance (TPM)?
Introduction
Total Productive Maintenance (TPM) is a process in which a workplace will utilise machines, equipment and its employees to continuously maintain production and reduce downtime. This process allows all employees working on a production line to become proactive whilst on the job, and carry out preventative maintenance that does not always require a specialist maintenance engineer. By doing this, it reduces the likeliness of a machine breaking down unexpectedly, saving your business potentially thousands on expensive repair bills. The addition of this process will improve your company’s Overall Equipment Effectiveness (OEE), the best practice metric which identifies the percentage of planned production time that is truly productive, as TPM will increase the amount of uptime that the line delivers during a shift.
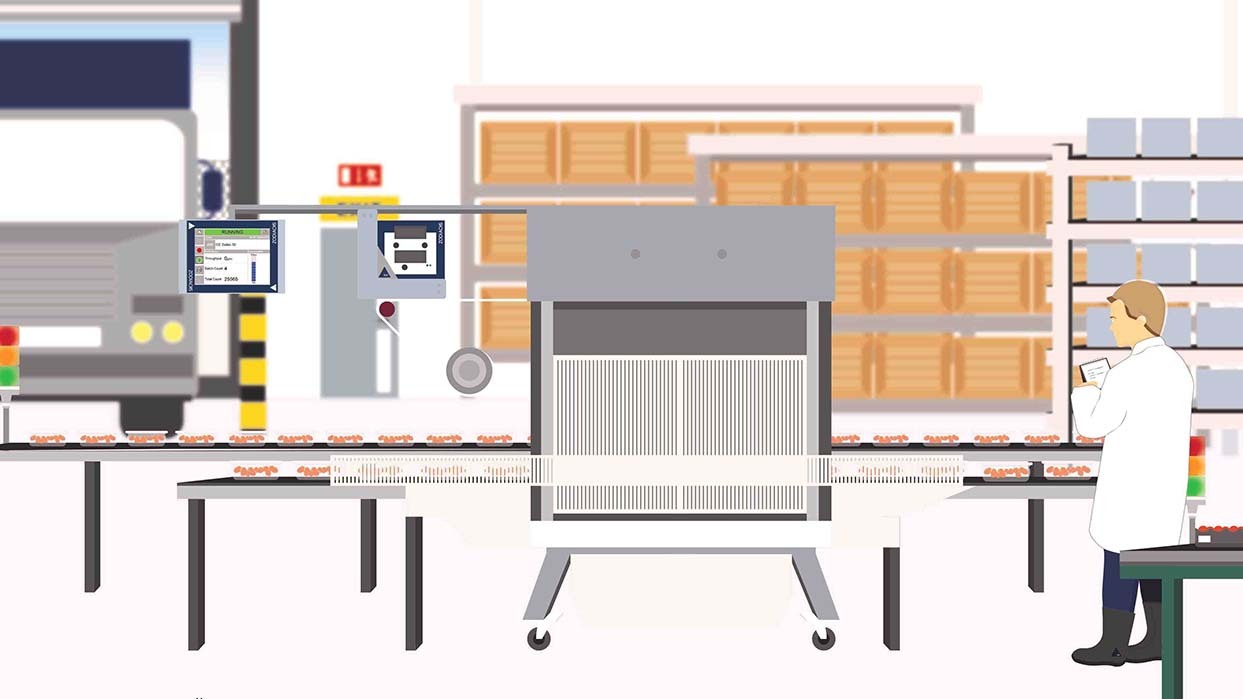
What are the types of preventative maintenance?
Time-based maintenance: With all of your equipment, it’s important to inspect the manufacturer’s guidance on time-based maintenance. This will vary based on the type of equipment, and will affect the frequency, the time to take the maintenance out including days, weeks, months and years. This can be as simple as regular basic checks for your equipment as well as scheduled cleaning.
Usage based maintenance: It goes without saying that the more that your equipment is used the more likely it will need some form of maintenance over a period of time. It would be worthwhile tracking the usage of your equipment, checking for any problematic trends within your production so you can plan ahead of time.
Predictive maintenance: It is essential that you record the performance of your production line so that when an anomaly happens you are able to identify this as soon as possible, giving you valuable insight to resolve the issue before it needs an expensive repair.
Prescriptive maintenance: Slightly more advanced, prescriptive maintenance uses analytics, machine learning, and artificial intelligence (AI) to make recommendations to improve operations, and to spot anomalies early for your team to action. For more information on smart factories and automation, download our guide on Industry 4.0.
The 8 pillars to Total Productive Maintenance
When considering a process for preventative maintenance, it would be a good idea to consider how each type can be contributed to by each member of your operation, including the operators who are working on the machines for the majority of their shifts. How can this be done? There are 8 pillars to Total Productive Maintenance which, once established and rolled out within a factory, will improve productivity and reduce downtime from preventing breakdowns. The 8 pillars are as follows:
- Autonomous Maintenance: These are the basic maintenance tasks that operators can action as part of their daily responsibilities. These include simple maintenance tasks like cleaning, inspecting the equipment for anything out of the ordinary that they can report to the maintenance team and other tasks set out by the responsible employee that does not require specialist attention. There are multiple benefits from this type of maintenance for both the factory and the operators in particular. The operators become more skilled and have more awareness of the machines that they are working on, whilst this frees up any time for the maintenance team to carry out work on more skilled and time precious tasks.
- Planned Maintenance: Linking back to preventative maintenance, there are multiple things to consider when planning in maintenance. Refer back to the manufacturer’s instructions on when critical planned maintenance is required, like servicing of the machines, which can also keep the warranty of the machine valid if it is still within its warranty period. Also, by tracking the performance of your machines, you can gain qualitative data that will give factories insight on how your production is performing. By scheduling in maintenance, you know when to expect some downtime and can plan this around your busiest times rather than leaving the machine to breakdown at any moment for your team to be reactive to.
- Quality Maintenance: By ensuring that equipment is able to detect and prevent errors during your production, you are able to stop defects moving further down the line and preventing any rework needed. By upgrading your equipment, which checks for the quality of each product running through the line, you are also able to perform a Route Cause Analysis (RCA), which helps your team identify what is causing issues, meaning you can plan downtime appropriately rather than spending too much time trying to figure out what the issue might be and using trial and error.
- Focused Improvement: This process involves getting a mixture of people from within a factory to assess current production and to suggest improvements based on what they see on a daily basis. By getting different viewpoints, suggested improvements can be assessed in several different ways and either be supported or opposed rationally based on the hypothesis and where the member of the team sits within the operation. Focused Improvement does not always mean that the change has to be a big one. Having an ‘always on’ approach to this can lead to healthy and incremental changes that over a period of time will eventually make a huge difference to production.
- Early Equipment Maintenance: Assessing previous equipment that was used within production can be a great basis for how you would like new equipment to be futureproofed for your operation by eradicating past pain-points. When requesting new equipment from your suppliers, make them aware of any pain points that you believe can either be removed or replaced. This could perhaps require a new design for the machine you would like to use within your operation.
- Education and Training: A vital part of being able to make this process work is ensuring that all staff are appropriately trained to take out any of the tasks assigned to them through TPM. Although certain tasks will not require specialist attention, incorrect procedures will be counterproductive and can cause further damage and downtime to the equipment. As well as the tasks, it is also about making sure that all members of the operation team, including operators and managers are fully aware of TPM and the process in place. If members of the team are not aligned on each pillar of TPM, the process could break down.
- Health, Safety & Environment: As with all changes within a factory, it is absolutely critical that Healthy and Safety measures are in place to ensure that all members of the team feel safe and comfortable whilst working. By providing your team an environment that is fully equipped with the appropriate Health and Safety requirements, they will be able to perform each of their tasks to the best of their ability, knowing that they will be safe from any harm. When a TPM process is in place, it is also important to consider Health and Safety precautions during the Training and Education stage.
- TPM in Office Functions: To align with the factory functions, it is a good idea to make sure that members of the team within the office are considering TPM with their tasks, especially if those actions have an impact of the factory floor, e.g. when ordering materials needed for production. By doing this, your team are fully aligned on operations, thus improving workflow.
How to implement Total Productive Maintenance
To roll out TPM successfully, there is a 5 step process that needs to be adhered to.
- Piloting: To start with, you should find a pilot area within your production to trial TPM. By piloting, you are able to see if there are any long term benefits of doing this by looking at the cost of implementation vs. the value you get from it doing it. A good place to start would be within small, less critical area as a steady way of measuring. Once you have calculated the ROI from the implementation, you can start to implement elsewhere within your factory functions.
- Restore equipment back to basic condition: It is important to make sure that the equipment you are using is working as expected to be able to measure the overall benefit of the new process in a fair way, especially during the piloting stage.
- OEE tracking: To ensure clear impact of TPM on your OEE, it’s important that you track this effectively in the first instance before you attribute uptime purely on TPM. We have a guide on how to identify each aspect of OEE and on how to improve this which you can read here. Once you fully understand OEE and how all different functions of your production line effect this, you should be able to see how TPM is improving the Availability, Performance and Quality of your operation.
- Reduce Major Losses: Referring back to the Focussed Improvement pillar of TPM, ensure that the data collated from your workforce and OEE reports becomes actionable in reducing any losses that your current operation is making.
- Planned Maintenance: Well into the TPM process, planned maintenance is a result of constant measurement of your production line. With the data you now have on your machines, you will be able to accurately judge when the appropriate times for maintenance can take place.
After you have followed the steps of implementation, you should have a fully effective TPM process in place.
Summary
Total Productive Maintenance (TPM) is a process in which a workplace will utilise machines, equipment and its employees to continuously maintain production and reduce downtime. A result of a strong TPM process will have a positive impact on your productions OEE, the best practice metric which identifies the percentage of planned production time that is truly productive, as TPM will increase the amount of uptime that the line delivers during a shift.
There are different types of preventative maintenance that can be carried out in factory functions, with the TPM process covering each. To be successful with TPM, it is crucial that you follow the 8 pillars set out in this process, starting with a thorough 5 step implementation period before being able to set up to tackle each pillar.
Related Articles
How to calculate Overall Equipment Effectiveness (OEE)
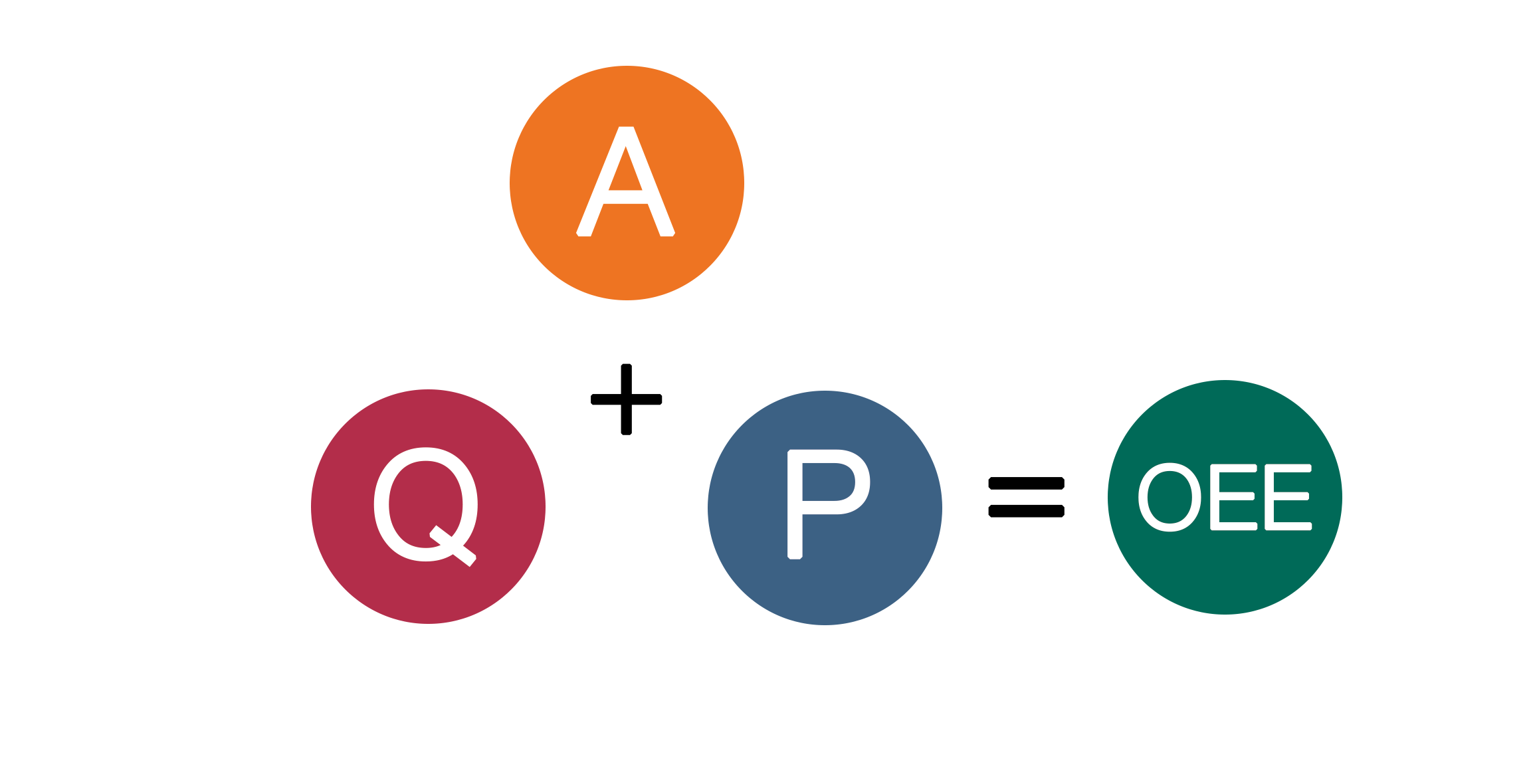