How to calculate Overall Equipment Effectiveness (OEE)
Introduction
Overall Equipment Effectiveness (OEE) is a term that is very much in vogue at the moment. And clearly the ability to accurately measure the efficiency of production lines is of huge benefit. However, as with many of these types of processes and procedures, it is easy to pay lip-service to them without fully embracing their principles or carrying them out to the necessary level of detail in order to achieve noticeable results.
In a world full of acronyms and awash with consultants, some factory personnel may even regard such measurement tools with a degree of suspicion, and as another layer of bureaucracy that gets in the way of them doing their jobs.
For OEE to deliver the best results, it is vital that everyone buys into it and understands the benefits it can offer as part of their daily routines.
What is OEE?
OEE is a best practice metric which identifies the percentage of planned production time that is truly productive. An OEE score of 100% represents perfect production: manufacturing only good packed products, as fast as possible and with no downtime.
The good news is that OEE measuring recognises that a 100% score can be very difficult for most companies to achieve. An OEE of 85% is therefore considered world class. More typically many manufacturers will be operating with an OEE of around 60%; for some it can be as low as 40%. This is precisely why OEE measuring is used, in order to enable them to more easily identify areas for improvement.
How is OEE measured?
In order to calculate a figure for these three factors, it is necessary to establish why they do not operate at 100%. OEE is calculated by combining the following three criteria:
- Availability: the amount of uptime that the line delivers during a shift.
- Performance: the actual speed of the line.
- Quality: the amount of packs that finally reach the customer as opposed to those that were rejected.
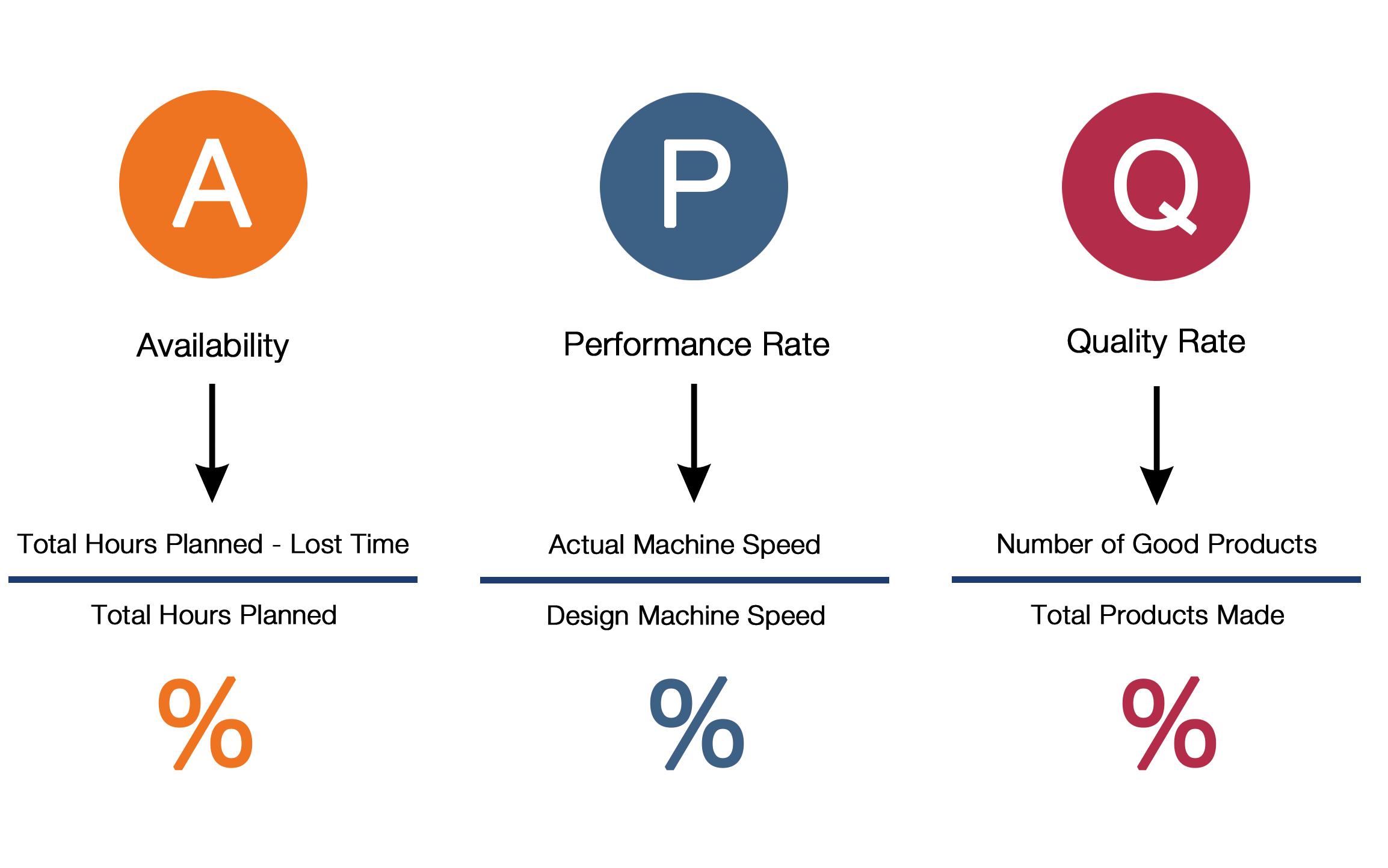
Availability
Availability, for example, takes into account the reasons why a line has not run continuously during a shift. These are defined as ‘Availability Losses’. Typical examples of these are equipment failures, adjustments and product changeovers.
Performance
Similarly, performance is measured by calculating ‘Performance Loss’, which accounts for anything that causes the manufacturing process to run at less than the maximum possible speed. Examples of Performance Losses include machine wear, substandard materials, misfeeds, and jams.
Quality
Quality loss accounts for manufactured products or packs that do not meet the required standards, anything that has to be scrapped or reworked. This is similar to manufacturers reporting First Pass Yield, where good products are those that successfully pass through the manufacturing and packing process first time without needing any rework.
Improving and measuring OEE
Making use of measurements
Ultimately, the point of OEE is not just about measuring it; it is also about improving and maximising your OEE. Therefore, identifying the causes for the various ‘losses’ provides the starting point for finding effective solutions to reduce or eliminate these.
This is the reason why product changeovers – or 'Planned Stoppages' – are included as a loss in the calculation of Availability, because these take up time that could otherwise be used for manufacturing. Although changeovers are a necessity on most production lines, meaning it will not be possible to completely eliminate them, there may well be opportunities to significantly reduce the time they take.
Improving OEE
The starting point for improving OEE is to identify and deal with the reasons for line downtime, loss of speed or rejected pack. The OEE process has identified what are termed the six ‘big losses’ that cause inefficiency in manufacturing. These are breakdowns, set-up and adjustments, small stops, reduced speed, start-up rejects, and production rejects.
How can you improve OEE?
To deal effectively with these losses – and also to identify areas where there are opportunities for further improvements or enhancements to be made – it is necessary to examine every part of the line. Ultimately, its overall performance will only be as strong as the weakest piece of equipment. However, the critical consideration is to look beyond the ‘functionality’ of each machine – what it was purchased and installed to do – and consider how it can also deliver ‘added value’ in terms of the overall running of the entire line.
This is particularly important where a machine may have been purchased due to external factors – to meet a specific customer or regulatory requirement for example. This can mean that it is regarded more as a ‘necessary evil’ rather than being considered for any additional benefits it can bring to the process.
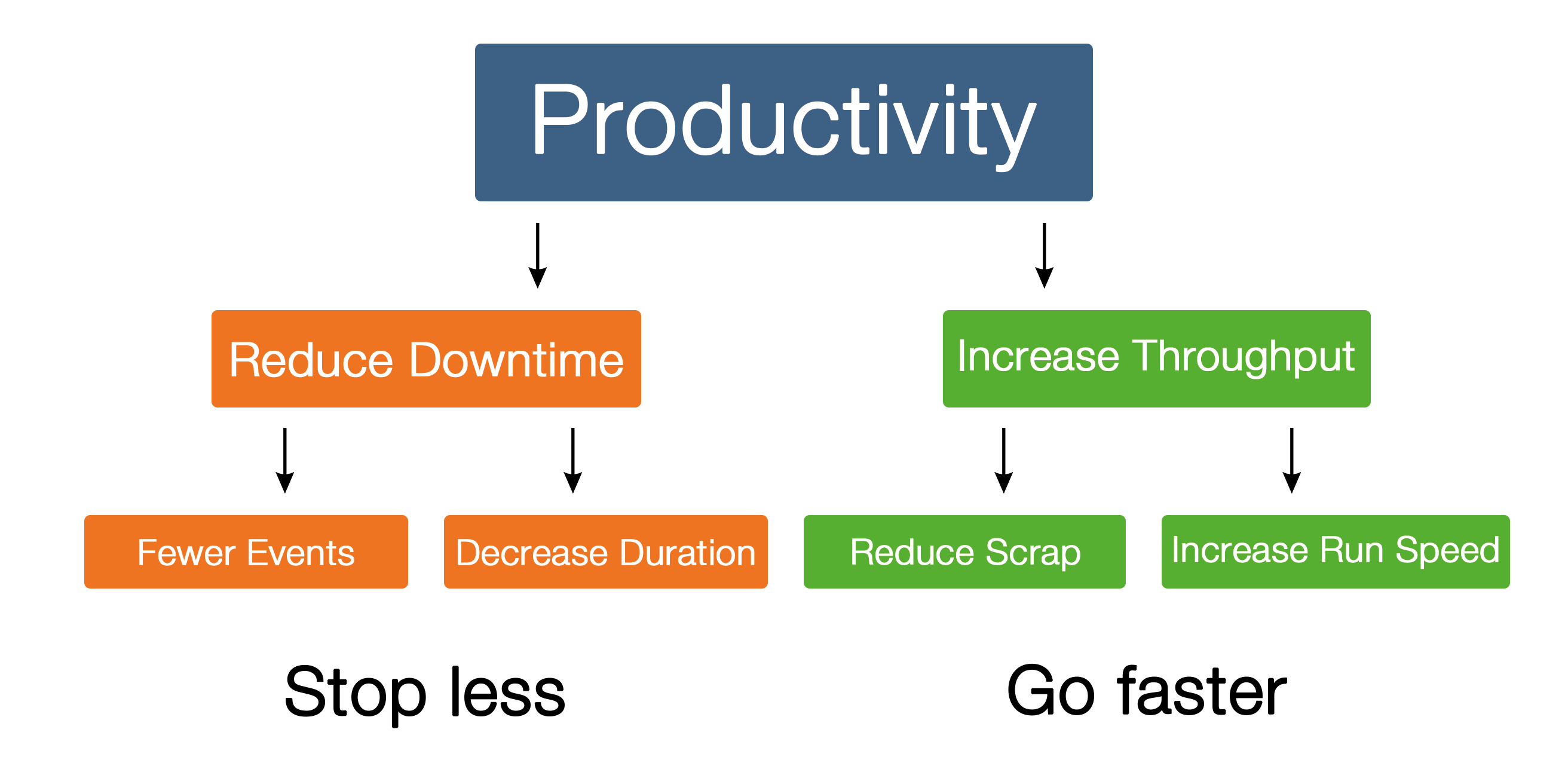
How can coding equipment help?
While the primary purpose of coding equipment may be to include information such as use by dates or batch codes as part of legislative or retailer requirements, it can also help to improve efficiencies and performance through areas such as ease of set-up, reliability and speed of operation, and even in some latest models, the monitoring of code quality.
The role of coders
Availability
Latest coders incorporate features that can reduce both planned and unplanned downtime. These include machines with fewer moving or wear parts that require periodic replacement; longer intervals between servicing; and easier maintenance procedures such as fast consumables changes and washdown designs that protect against dust and water ingress.
Product changeovers have been made quicker and generate fewer mistakes with coders that can store multiple presets to allow code changes at the touch of a button. Many coders are also able to deliver clear, repeatable quality codes, even after a long stoppage.
Code creation has become more intuitive and mistake-proof, with the introduction of touch screen user interfaces and onscreen help and prompts. Editing capabilities can be limited for different users and set-up can be accessed and controlled remotely.
Performance
Advances across the different coding technologies have focused on increasing printing speeds while maintaining code quality. In Thermal Transfer Overprinting (TTO) for example, the ability to print in both intermittent and continuous motion on the same machine enables speeds to be matched to differing requirements, and the elimination of mechanical wear parts such as clutches and brakes enhances long-term reliability.
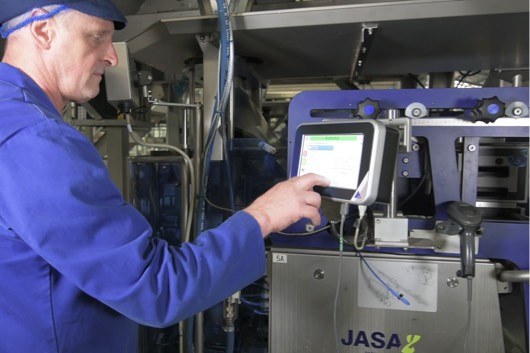
Latest innovations in print and apply labelling have seen the introduction of machines that print and directly apply a label to a pack in a continuous action without the need for a tamp applicator or compressed air. This allows the machine to print at the speed of the line, even when packs are very closely spaced together, without ever missing a pack.
Self-maintaining printhead systems for case coders automatically clean and re-prime the printhead before every single product is printed without slowing down the production line.
Quality
A legible code is essential to enable a pack to meet relevant compliance and regulations. A well-presented code will also not detract from the overall pack design and appearance so that brand image is not compromised in any way.
Ensuring any problems with a code are detected before a pack leaves the factory usually requires a separate vision system on the line. However, defining the quality parameters for the code can be challenging. If they are too restrictive, this can lead to many acceptable codes being rejected, affecting efficiency rates. These systems are also unable to monitor and identify a gradual deterioration in code quality, which may allow some unacceptable quality codes to pass through the system undetected before the reject mechanism comes into action.
To provide a more accurate and consistent measurement, some new generation coders are now able to monitor and report on the quality of each code as it is produced. Importantly, this provides the necessary early warning of any potential loss of code quality. In this way, operators can take immediate action to rectify a problem and therefore minimise production downtime and disruption.
What can I do with this information?
Many coders incorporate a range of reporting functions. Information can be viewed on screen or accessed and printed off remotely. This feedback can be used as part of an overall assessment of line performance in order to help identify ways to improve productivity and efficiency.
OEE for everyone
The benefits of OEE are most easily appreciated by those with responsibility for production, thanks to its ability to help deliver improved performance, efficiency and throughput.
The Finance department
The finance department too will be able to see how such improvements translate into higher numbers on the bottom line.
Company reputation
High quality packs leaving the factory will greatly help to minimise the risk of product recalls or retailer rejects, with the resulting additional costs and fines that these may incur, as well as the damage to a company’s reputation.
On the production line
It is equally essential to help those at the sharp end on the factory floor see how OEE can make daily tasks a little easier.
Here it is important also to emphasise how the functionality of the equipment is helping to deliver performance efficiencies. For example, intuitive icon-based screens and fast and easy changing of consumables on coders will make set-up and changeover procedures much easier. Early warning of problems and on-screen prompts to help resolve them will minimise the need for manual interventions. Consistent throughput of quality in-spec packs minimises the need for reworking.
Use of charts and graphs are useful in explaining where problems lie, which can be a major first step in achieving the buy-in from everyone to find the appropriate solution.
Example OEE loss chart
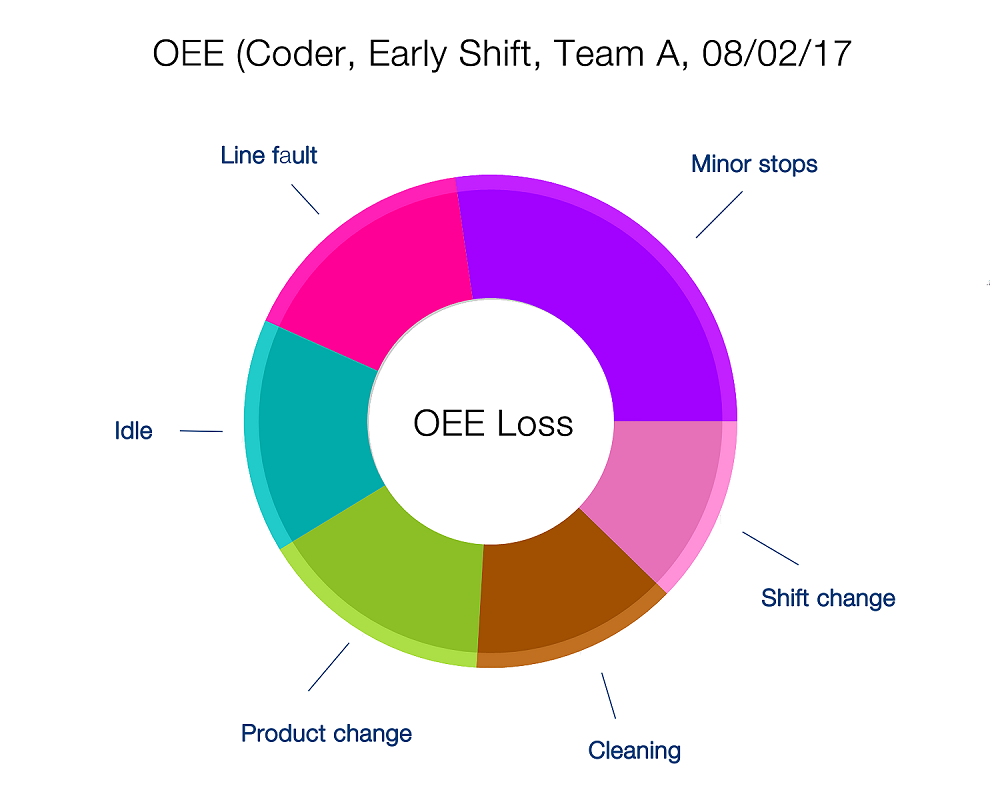
Related Articles
What is Total Productive Maintenance (TPM)?
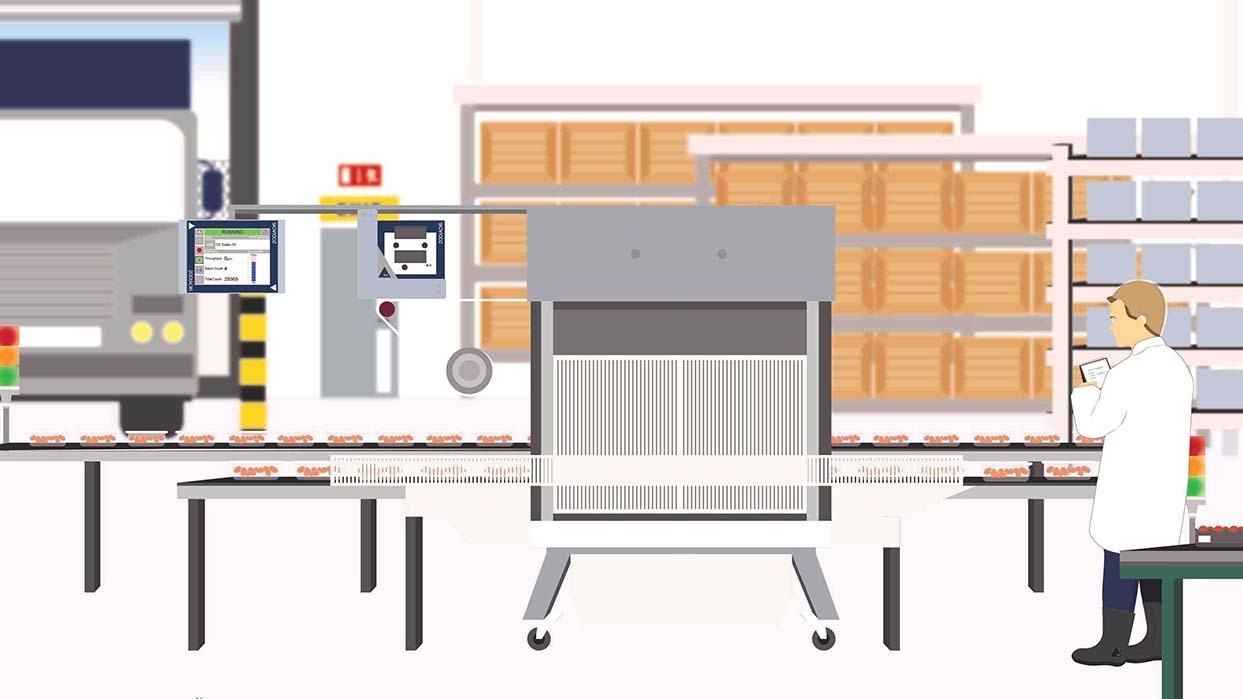
Get in touch
Ready to improve your operation's OEE? We may be able to help, so please get in touch with one of our experts today.